Shock-proof automatic equipment frame
A technology of automation equipment and frame, applied in the direction of mechanical equipment, engine base, spring/shock absorber, etc., can solve the problems of device damage, single structure, shortened service life, etc., and achieve the effect of reducing vibration
- Summary
- Abstract
- Description
- Claims
- Application Information
AI Technical Summary
Problems solved by technology
Method used
Image
Examples
Embodiment Construction
[0013] The technical solutions in the embodiments of the present invention will be clearly and completely described below in conjunction with the accompanying drawings in the embodiments of the present invention. Obviously, the described embodiments are only a part of the embodiments of the present invention, rather than all the embodiments. Based on the embodiments of the present invention, all other embodiments obtained by those of ordinary skill in the art without creative work shall fall within the protection scope of the present invention.
[0014] See figure 1 , The present invention provides a technical solution: an earthquake-resistant automation equipment frame, comprising a base 1 and a frame 2. The upper surface of the base 1 is fixedly connected with uniformly distributed first sleeves 3, and the inner side walls of the first sleeves 3 are slidingly connected There is a second sleeve 4, the upper surface of the second sleeve 4 is fixedly connected with a clamping plat...
PUM
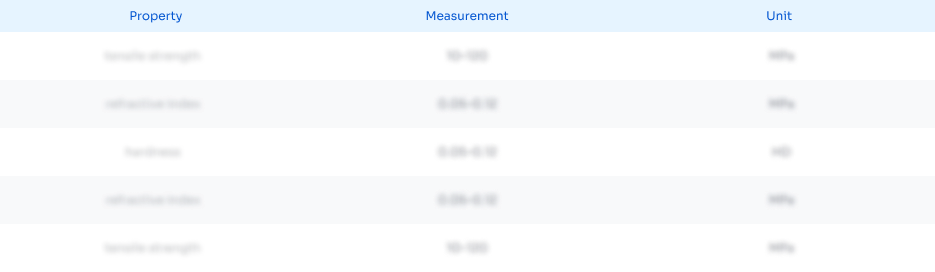
Abstract
Description
Claims
Application Information

- Generate Ideas
- Intellectual Property
- Life Sciences
- Materials
- Tech Scout
- Unparalleled Data Quality
- Higher Quality Content
- 60% Fewer Hallucinations
Browse by: Latest US Patents, China's latest patents, Technical Efficacy Thesaurus, Application Domain, Technology Topic, Popular Technical Reports.
© 2025 PatSnap. All rights reserved.Legal|Privacy policy|Modern Slavery Act Transparency Statement|Sitemap|About US| Contact US: help@patsnap.com