Measurement and calibration integrated marine fiber bragg grating strain sensor system
A technology of strain sensor and optical fiber grating, which is applied in the direction of using optical devices, instruments, measuring devices, etc., can solve the problems of inconvenience, insufficient sensor traceability system, and the lack of multiple installation and calibration of sensors, so as to achieve convenient use, Guarantee the effect of state consistency and stability
- Summary
- Abstract
- Description
- Claims
- Application Information
AI Technical Summary
Problems solved by technology
Method used
Image
Examples
Embodiment Construction
[0020] The present invention will be further described below in conjunction with drawings and embodiments.
[0021] Such as figure 1 , as shown in 2, a marine fiber grating strain sensor system integrating measurement and calibration is composed of two parts: a fiber grating strain sensor and a sensor installation tool (calibration device), wherein the fiber grating strain sensor includes a sensor fixed end 1 and a sensor movable end 2 , protective steel pipe 3, fiber grating 4, fixed end welding base 8, movable end welding base 9, installation tool (calibration device) including positioning plate 5, high-precision differential screw rod 6, return spring 7.
[0022] One end of the pigtail fiber of the fiber grating 4 is fixed on the fixed end 1 of the sensor, and the other end is fixed on the movable end 2 of the sensor. The distance between the two points of the fixed fiber grating 4 is the effective strain length L, and the middle of the fiber grating 4 is protected by a pro...
PUM
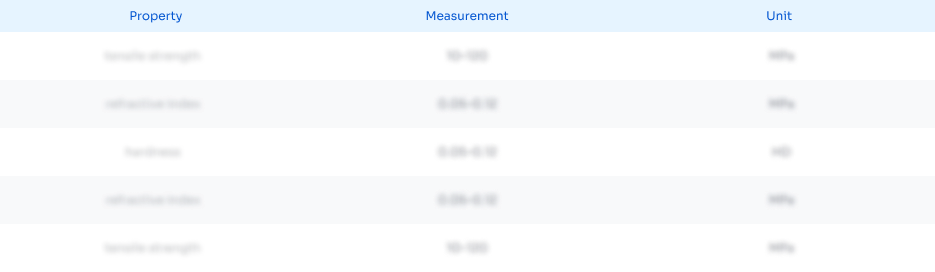
Abstract
Description
Claims
Application Information

- Generate Ideas
- Intellectual Property
- Life Sciences
- Materials
- Tech Scout
- Unparalleled Data Quality
- Higher Quality Content
- 60% Fewer Hallucinations
Browse by: Latest US Patents, China's latest patents, Technical Efficacy Thesaurus, Application Domain, Technology Topic, Popular Technical Reports.
© 2025 PatSnap. All rights reserved.Legal|Privacy policy|Modern Slavery Act Transparency Statement|Sitemap|About US| Contact US: help@patsnap.com