Method and device for controlling asymmetric flatness of oriented silicon steel
A technology of oriented silicon steel and flatness, which is applied in the field of control of asymmetric flatness of oriented silicon steel, can solve the problem of increasing the cut loss rate of strip steel in downstream production lines, the inability to effectively control the asymmetric flatness of silicon steel, and poor control accuracy And other issues
- Summary
- Abstract
- Description
- Claims
- Application Information
AI Technical Summary
Problems solved by technology
Method used
Image
Examples
Embodiment 1
[0038] This embodiment provides a method for controlling the asymmetric flatness of grain-oriented silicon steel, such as figure 1 The methods shown include:
[0039] S110, controlling the furnace entry temperature of the oriented silicon steel slab to be greater than 350°C;
[0040] In order to reduce the blockage rate of asymmetric flatness of oriented silicon steel, control the furnace temperature of oriented silicon steel slab to be higher than 350°C. If hot charging and direct loading cannot be guaranteed; within 5°C. In this way, the asymmetric flatness blocking rate of grain-oriented silicon steel can be reduced by more than 15%.
[0041] S111. In the heating stage, control the preheating temperature of the heating furnace to be 800-950°C, control the temperature of the first heating section of the heating furnace to be 1070-1090°C, and control the temperature of the second heating section of the heating furnace. The temperature is 1130-1150°C, the temperature of the...
Embodiment 2
[0075] This embodiment provides a control device for the asymmetric flatness of grain-oriented silicon steel, such as figure 2 As shown, the device includes: a first control unit 21, a second control unit 22, a third control unit 23, a fourth control unit 25, a fifth control unit 26 and a sixth control unit 27; wherein,
[0076] In order to reduce the blockage rate of asymmetric flatness of oriented silicon steel, the first control unit 21 is used to control the temperature of the oriented silicon steel slab to be higher than 350°C. Keep warm, and control the difference between furnaces within 5°C. In this way, the asymmetric flatness blocking rate of grain-oriented silicon steel can be reduced by more than 15%.
[0077]In the heating stage, the heating process of the oriented silicon steel slab needs to be slow, the slab outlet temperature is strictly controlled at 1122-1128°C, and the temperature difference of each slab should be eliminated in the second heating section of...
Embodiment 3
[0101] In actual application, when rolling oriented and high-grade non-oriented silicon steel on the 1580 hot continuous rolling production line of Shougang Qiangang, the specific implementation is as follows:
[0102] Control the temperature of the oriented silicon steel slab into the furnace to be greater than 350°C. In the heating stage, control the temperature of the preheating section to 850°C; the temperature of the first heating section to 1090°C, the temperature of the second heating section to 1140°C, The temperature is 1130°C; the furnace pressure of the control furnace is 26pa.
[0103] In order to reduce the temperature drop in the rough rolling process, after the slab is released from the furnace, during the rough rolling process, the rough rolling mode of the rough rolling stand is controlled as "0+5" rolling mode; here, the rough rolling stand includes the first rough rolling stand and the second roughing stand; the "0+5" rolling mode includes: the first roughin...
PUM
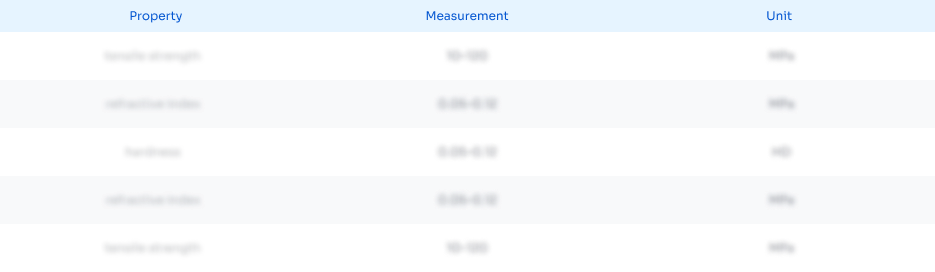
Abstract
Description
Claims
Application Information

- R&D
- Intellectual Property
- Life Sciences
- Materials
- Tech Scout
- Unparalleled Data Quality
- Higher Quality Content
- 60% Fewer Hallucinations
Browse by: Latest US Patents, China's latest patents, Technical Efficacy Thesaurus, Application Domain, Technology Topic, Popular Technical Reports.
© 2025 PatSnap. All rights reserved.Legal|Privacy policy|Modern Slavery Act Transparency Statement|Sitemap|About US| Contact US: help@patsnap.com