Sand mold casting device for sand core production
A sand mold and sand core technology is applied in the field of sand mold casting devices for sand core production, which can solve the problems of high failure rate, inability to ensure that the casting material is completely filled with membrane shells, etc., and achieve the effect of speeding up the feeding
- Summary
- Abstract
- Description
- Claims
- Application Information
AI Technical Summary
Problems solved by technology
Method used
Image
Examples
Embodiment Construction
[0025] The following will clearly and completely describe the technical solutions in the embodiments of the present invention with reference to the accompanying drawings in the embodiments of the present invention. Obviously, the described embodiments are only some, not all, embodiments of the present invention. Based on the embodiments of the present invention, all other embodiments obtained by persons of ordinary skill in the art without making creative efforts belong to the protection scope of the present invention.
[0026] Such as Figure 1-Figure 6 As shown, this specific embodiment adopts the following technical scheme: it includes a box body 1, a foot 2, a feeding mechanism 3, a fixing mechanism 4, a vibration mechanism 5 and a door body 6, and the four corners of the lower surface of the box body 1 are welded and fixed There are feet 2, and the upper side of the box body 1 is provided with a feeding mechanism 3, and the feeding mechanism 3 is fixed by a feeding pipe 3...
PUM
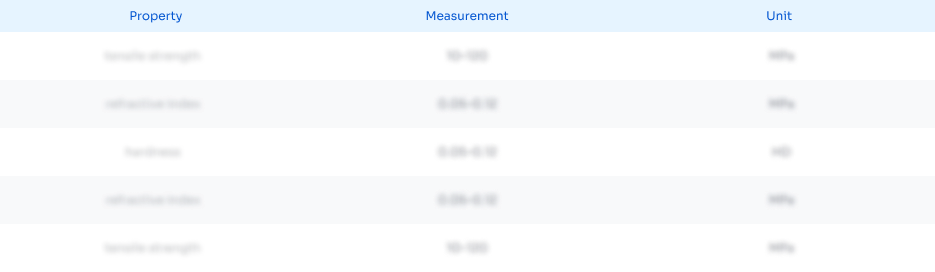
Abstract
Description
Claims
Application Information

- R&D
- Intellectual Property
- Life Sciences
- Materials
- Tech Scout
- Unparalleled Data Quality
- Higher Quality Content
- 60% Fewer Hallucinations
Browse by: Latest US Patents, China's latest patents, Technical Efficacy Thesaurus, Application Domain, Technology Topic, Popular Technical Reports.
© 2025 PatSnap. All rights reserved.Legal|Privacy policy|Modern Slavery Act Transparency Statement|Sitemap|About US| Contact US: help@patsnap.com