Maintenance system for gear flaw detection
A technology for flaw detection and gears, which is applied in measuring devices, using sound waves/ultrasonic waves/infrasonic waves to analyze solids, and using sound waves/ultrasonic waves/infrasonic waves for material analysis, etc., can solve problems that affect the detection effect and cannot detect gear flaws, and achieve Ensure perfect meshing, improve the effect of detection, and meet the effect of flaw detection
- Summary
- Abstract
- Description
- Claims
- Application Information
AI Technical Summary
Problems solved by technology
Method used
Image
Examples
Embodiment 1
[0028] see figure 1 , image 3 , Figure 4 and Figure 5 , the present invention provides a technical solution: a maintenance system for gear flaw detection, including a base 1, a chassis 2 and a flaw detector, the chassis 2 is fixedly installed on the upper end of the base 1, and one side of the outer wall of the base 1 is fixedly installed There is a PLC controller 5, a box door is mounted on a hinge on one side of the outer wall of the cabinet 2, and a No. 1 motor 6 and a bearing seat 7 are fixedly installed on one side of the inner bottom of the cabinet 2, and the bearing seat 7 is provided with two groups. A threaded rod 14 is rotated between the bearing blocks 7, and a threaded slide 13 is mounted on the external thread of the threaded rod 14. The upper end of the threaded slide 13 is fixed with a support rod 12 through a loading plate, and the upper end of the support rod 12 is The gear 19 to be tested is mounted on the external rotation, and the other side of the in...
Embodiment 2
[0039] see Figure 2-5 , the present invention provides a technical solution: a maintenance system for gear flaw detection, including a base 1, a chassis 2 and a flaw detector, the chassis 2 is fixedly installed on the upper end of the base 1, and one side of the outer wall of the base 1 is fixedly installed There is a PLC controller 5, a box door is mounted on a hinge on one side of the outer wall of the cabinet 2, and a No. 1 motor 6 and a bearing seat 7 are fixedly installed on one side of the inner bottom of the cabinet 2, and the bearing seat 7 is provided with two groups. A threaded rod 14 is rotated between the bearing blocks 7, and a threaded slide 13 is mounted on the external thread of the threaded rod 14. The upper end of the threaded slide 13 is fixed with a support rod 12 through a loading plate, and the upper end of the support rod 12 is The gear 19 to be tested is mounted on the external rotation, and the other side of the inner bottom of the cabinet 2 is fixedl...
PUM
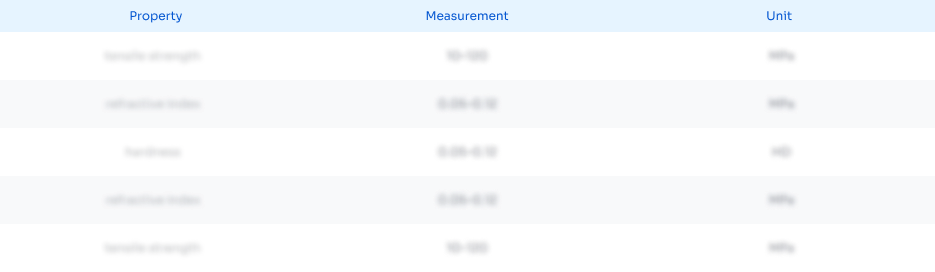
Abstract
Description
Claims
Application Information

- Generate Ideas
- Intellectual Property
- Life Sciences
- Materials
- Tech Scout
- Unparalleled Data Quality
- Higher Quality Content
- 60% Fewer Hallucinations
Browse by: Latest US Patents, China's latest patents, Technical Efficacy Thesaurus, Application Domain, Technology Topic, Popular Technical Reports.
© 2025 PatSnap. All rights reserved.Legal|Privacy policy|Modern Slavery Act Transparency Statement|Sitemap|About US| Contact US: help@patsnap.com