Roughness detection robot for precision machining and detection method thereof
A technology of precision machining and roughness, which is applied in the field of precision machining roughness detection robot and its detection. The effect of precision
- Summary
- Abstract
- Description
- Claims
- Application Information
AI Technical Summary
Problems solved by technology
Method used
Image
Examples
Embodiment 1
[0032] see figure 1 , figure 2 and image 3 , a roughness detection robot for precision machining, comprising a transmission frame 2 and a conveyor belt 5, the conveyor belt 5 is provided with a bearing jig 4, the transmission frame 2 is equipped with a detection mechanism 1, and the detection The main body of the mechanism 1 is a detection barrel 11, the detection barrel 11 is a cylindrical structure, and several detection frames 12 are equidistantly installed on the outer wall of the detection frame 11, and the detection frames 12 pass through the fixed substrate 13 is installed on the outer wall of the detection machine barrel 11. Several detection brackets 14 are independently arranged on the detection frame 12. The front end of the detection bracket 14 is equipped with a detection head 15, and the detection head 15 is inserted through the movable sleeve 16. Installed on the detection bracket 14, the inner cavity of the detection bracket 14 is provided with a fixed rod ...
Embodiment 2
[0037]Please refer to Fig. 5, the present embodiment is further optimized as embodiment one, on its basis, the both sides of described conveyor belt 5 are all equipped with supporting plate 38, and lifting frame 3 is all installed on described supporting plate 38 , the lifting guide rail 31 is installed on the lifting frame 3, the sliding seat 32 is installed on the lifting guide rail 31, the sliding seat 32 is installed on the notch of the lifting guide rail 31 through the roller 33, and the lifting frame 3 Lifting screw rods 34 are all installed, and threaded sleeves 36 are installed on the inner side of the sliding seat 32, and the lifting screw rods 34 are all pierced in the screw holes of the corresponding threaded sleeves 36, and the tops of the lifting screw rods 34 are equipped with transmission The wheel 35 is connected by a synchronous belt 37 between the transmission wheels 35 on both sides.
[0038] The application is provided with a lifting frame 3 to drive the tr...
Embodiment 3
[0040] see Figure 6 , this embodiment is further optimized as Embodiment 1. On the basis of it, a leveling mechanism 41 is installed on the bottom of the carrying jig 4, and bending frames 42 are installed at the four corners of the leveling mechanism 41. The four corners of the carrying fixture 4 are provided with corresponding support rods 43, and the support rods 43 are installed on the corresponding bending frame 42 through the movable shaft 44, and the angle measuring instrument 45 is installed on the bending frame 42, The angle measuring instrument 45 is provided with arc-shaped grooves 46 , and balls 47 are installed on the support rods 43 , and the balls 47 are embedded in the notches of the corresponding arc-shaped grooves 46 . Bending struts 48 are also installed at the four corners of the carrying jig 4 and the leveling mechanism 41 .
[0041] In view of the different shapes of the workpieces, and the inspection surface is not normally on the horizontal line, the ...
PUM
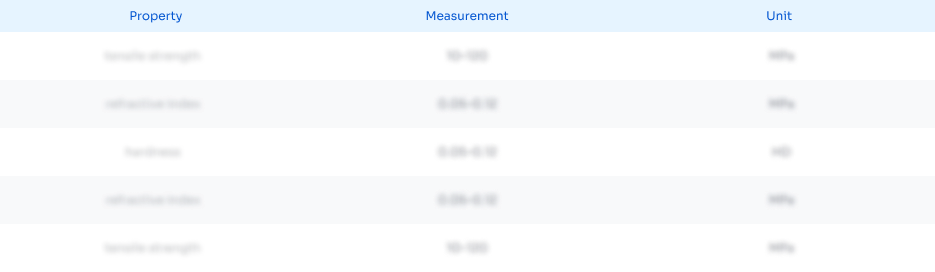
Abstract
Description
Claims
Application Information

- Generate Ideas
- Intellectual Property
- Life Sciences
- Materials
- Tech Scout
- Unparalleled Data Quality
- Higher Quality Content
- 60% Fewer Hallucinations
Browse by: Latest US Patents, China's latest patents, Technical Efficacy Thesaurus, Application Domain, Technology Topic, Popular Technical Reports.
© 2025 PatSnap. All rights reserved.Legal|Privacy policy|Modern Slavery Act Transparency Statement|Sitemap|About US| Contact US: help@patsnap.com