Special-shaped cutter mold and preparation method thereof
A cutting die and special-shaped technology, which is applied in the field of special-shaped cutting dies and its preparation, can solve the problems of unreasonable utilization of blades, increase of product defect rate, and reduction of material utilization rate, so as to improve material utilization rate, expand profit margin, reduce The effect of cutting pressure
- Summary
- Abstract
- Description
- Claims
- Application Information
AI Technical Summary
Problems solved by technology
Method used
Image
Examples
preparation example Construction
[0038] A method for preparing a special-shaped die, comprising:
[0039]The step of setting mold cavities: take the base of the knife mold, set a number of mold cavities arranged in an array on the base of the knife mold, and the adjacent two mold cavities in the same row or column are respectively recorded as the first mold cavity and the second mold cavity, and the second A mold cavity includes a first linear cavity and a first non-linear cavity, a second mold cavity includes a second linear cavity and a second non-linear cavity, and the first linear cavity and the second linear cavity completely overlap , the first non-linear mold cavity and the second non-linear mold cavity are connected left and right; the two opposite mold cavities in different rows or columns are respectively recorded as the first mold cavity and the third mold cavity, and the third mold cavity includes a third linear hole and a third non-linear hole, a gap is provided between the first linear hole and ...
Embodiment 1
[0043] like figure 2 As shown, a special-shaped knife mold includes a knife mold base 20, several mold cavities and several blades; several mold cavities are arrayed on the knife mold base 20 in the form of 18 rows and 4 columns; two adjacent mold cavities in the same column Respectively denoted as the first mold cavity 21 and the second mold cavity 22, the first mold cavity 21 includes the first linear cavity and the first non-linear cavity, and the second mold cavity 22 includes the second linear cavity and the second non-linear cavity shaped cavity, the first linear mold cavity and the second linear mold cavity completely overlap (see area A), and the first non-linear mold cavity and the second non-linear mold cavity are connected left and right (such as Figure 4 As shown, the common knife place is directly welded together, see area D); The two adjacent mold cavities facing each other are respectively marked as the first mold cavity 21 and the third mold cavity 23, and th...
Embodiment 2
[0045] like image 3 As shown, the difference between embodiment 2 and embodiment 1 is that the mold cavities are arrayed on the die matrix 20 in the form of 8 rows and 9 columns, and the adjacent two mold cavities in the same row are respectively marked as the first The mold cavity 21 and the second mold cavity 22, two adjacent rows of directly opposite mold cavities are respectively marked as the first mold cavity 21 and the third mold cavity 23.
[0046] Others are identical with specific embodiment 1.
PUM
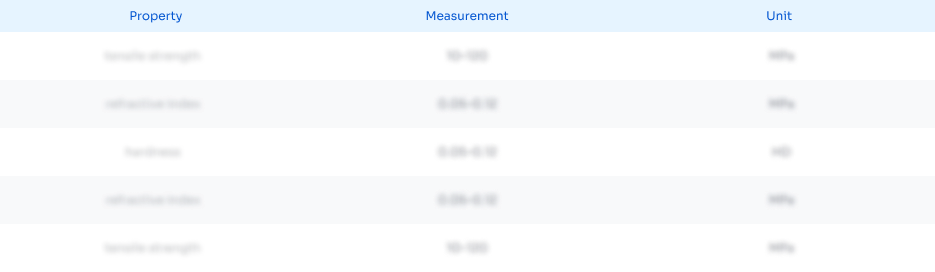
Abstract
Description
Claims
Application Information

- R&D
- Intellectual Property
- Life Sciences
- Materials
- Tech Scout
- Unparalleled Data Quality
- Higher Quality Content
- 60% Fewer Hallucinations
Browse by: Latest US Patents, China's latest patents, Technical Efficacy Thesaurus, Application Domain, Technology Topic, Popular Technical Reports.
© 2025 PatSnap. All rights reserved.Legal|Privacy policy|Modern Slavery Act Transparency Statement|Sitemap|About US| Contact US: help@patsnap.com