Directional guide mechanism, device, method and medium
A guide column, thickness direction technology, applied in brake actuators, devices for preventing/restricting/restoring the movement of parts of control mechanisms, mechanical control devices, etc. problems, to achieve the effect of a wide range of applications and high operating accuracy
- Summary
- Abstract
- Description
- Claims
- Application Information
AI Technical Summary
Problems solved by technology
Method used
Image
Examples
Embodiment 1
[0137] Such as Figure 5 As shown, the number of mobile unit assemblies 900 is one; the second mobile unit 902 is relatively fixed to the housing of the locking mechanism, for example, they are all fastened on the same rigid bracket, and for example, the second mobile unit 902 passes through The rigid bracket is firmly connected with the housing of the locking mechanism.
[0138] The locking mechanism includes a pair of clamping mechanisms 904 ; wherein, the wide ends 90411 are arranged oppositely between two clamping mechanisms 904 in the pair of clamping mechanisms 904 . In a variation example, the narrow ends 90412 of the paired clamping mechanisms 904 are arranged opposite to each other, for example, Image 6 shown.
[0139] Specifically, such as Figure 10 As shown, the locking mechanism includes a clamping mechanism 904; the clamping mechanism 904 includes a clamping chamber 9041, a clamping clip 9042, and a clip driver 9043;
[0140] The width of the clamping chambe...
Embodiment 2
[0156] Such as Image 6 shown, for Figure 5 change example. In this variation example, the narrow ends 90412 of the two clamping mechanisms 904 in the paired clamping mechanisms 904 are arranged opposite to each other.
[0157] exist Image 6 middle:
[0158] - To allow the first mobile unit 901 to slide freely to the left and right relative to the second mobile unit 902, the clamp clips 9042 in the left and right clamp mechanisms 904 are located at the wide end 90411 and the wide end 90411 respectively;
[0159] - To allow the first mobile unit 901 to slide freely to the left relative to the second mobile unit 902, the clamping parts 9042 in the left and right clamping mechanisms 904 are respectively located at the narrow end 90412 and the wide end 90411;
[0160] - To allow the first mobile unit 901 to slide freely to the right only relative to the second mobile unit 902, the clamp clips 9042 in the left and right clamp mechanisms 904 are respectively located at the wid...
Embodiment 3
[0163] Such as Figure 7 shown, for Figure 5 change example. In this variation example, two clamping mechanisms 904 in the pair of clamping mechanisms 904 are located on the same side of the first moving unit 901 .
[0164] exist Image 6 In a modified example, two clamping mechanisms 904 in the pair of clamping mechanisms 904 may also be located on the same side of the first moving unit 901 .
PUM
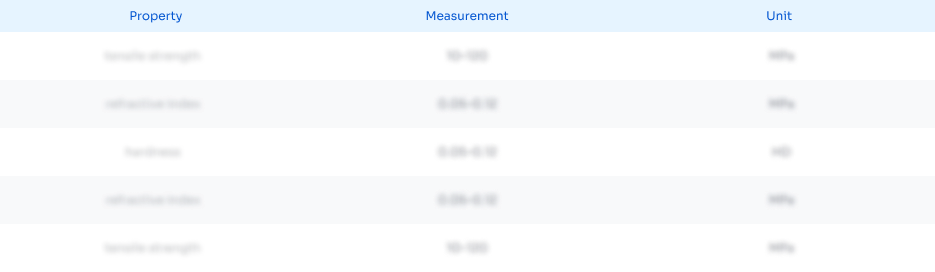
Abstract
Description
Claims
Application Information

- R&D
- Intellectual Property
- Life Sciences
- Materials
- Tech Scout
- Unparalleled Data Quality
- Higher Quality Content
- 60% Fewer Hallucinations
Browse by: Latest US Patents, China's latest patents, Technical Efficacy Thesaurus, Application Domain, Technology Topic, Popular Technical Reports.
© 2025 PatSnap. All rights reserved.Legal|Privacy policy|Modern Slavery Act Transparency Statement|Sitemap|About US| Contact US: help@patsnap.com