A two-component tile grout
A joint filling agent, two-component technology, applied in the direction of coating, can solve the problems of easy cracking and poor waterproofness of joint filling materials, and achieve the effect of solving easy cracking, enhancing water resistance and improving light curing effect.
- Summary
- Abstract
- Description
- Claims
- Application Information
AI Technical Summary
Problems solved by technology
Method used
Examples
preparation example Construction
[0027] The preparation method of mixed polymer is:
[0028] A. Put ethanol and tetraethoxysilane into the reaction kettle at a mass ratio of 26:10~13, use nitrogen protection, stir for 30 minutes, add 18-crown ether- 6 and a catalyst with a mass of 3-5% tetraethoxysilane, the temperature is raised to 160-170°C, the pressure is increased to 1.2-1.4MPa, and the reaction is stirred for 7-10 hours;
[0029] B. After the reaction is finished, cool to room temperature, discharge, collect the discharge, and take 130-160 parts of ethyl acetate, 40-50 parts of epoxy resin, 25-30 parts of discharge, 20-23 parts of acrylic acid, 18-22 parts of soybean oil, 10-19 parts of mixed monomers, 4-6 parts of benzyltriethylammonium chloride, 1-4 parts of azobisisobutylcyanide;
[0030] C. First, put ethyl acetate, epoxy resin, discharge material and soybean oil into the reactor, protect it with nitrogen, preheat at 40-50°C, add benzyltriethylammonium chloride, and raise the temperature to 110-115...
Embodiment 1
[0039] The catalyst is lithium hydroxide.
[0040] The mixed monomer is formed by mixing methyl methacrylate and γ-methacryloxypropyl trimethoxysilane at a mass ratio of 12:3.
[0041]The preparation method of mixed polymer is:
[0042] A. Put ethanol and tetraethoxysilane into the reaction kettle at a mass ratio of 26:10, use nitrogen protection, stir for 30 minutes, add 18-crown-6 and tetraethyl ether with 70% tetraethoxysilane quality For a catalyst with 3% oxysilane mass, the temperature was raised to 160 ° C, the pressure was increased to 1.2 MPa, and the reaction was stirred for 7 hours;
[0043] B. After the reaction is finished, cool to room temperature, discharge, collect the discharge, and in parts by weight, get 130 parts of ethyl acetate, 40 parts of epoxy resin, 25 parts of discharge, 20 parts of acrylic acid, 18 parts Soyoleic acid, 10 parts of mixed monomers, 4 parts of benzyltriethylammonium chloride, 1 part of azobisisobutylcyanide;
[0044] C. First, put e...
Embodiment 2
[0053] The catalyst is potassium hydroxide.
[0054] The mixed monomer is formed by mixing methyl methacrylate and γ-methacryloxypropyl trimethoxysilane at a mass ratio of 12:4.
[0055] The preparation method of mixed polymer is:
[0056] A. Put ethanol and tetraethoxysilane into the reaction kettle at a mass ratio of 26:12, use nitrogen protection, stir for 30 minutes, add 18-crown-6 and tetraethyl ether with 72% tetraethoxysilane quality For a catalyst with 4% oxysilane mass, the temperature was raised to 165 ° C, the pressure was increased to 1.3 MPa, and the reaction was stirred for 9 hours;
[0057] B. After the reaction is finished, cool to room temperature, discharge, collect the discharge, and in parts by weight, get 145 parts of ethyl acetate, 45 parts of epoxy resin, 28 parts of discharge, 21 parts of acrylic acid, 20 parts of Soyoleic acid, 15 parts of mixed monomers, 5 parts of benzyltriethylammonium chloride, 3 parts of azobisisobutylcyanide;
[0058] C. First...
PUM
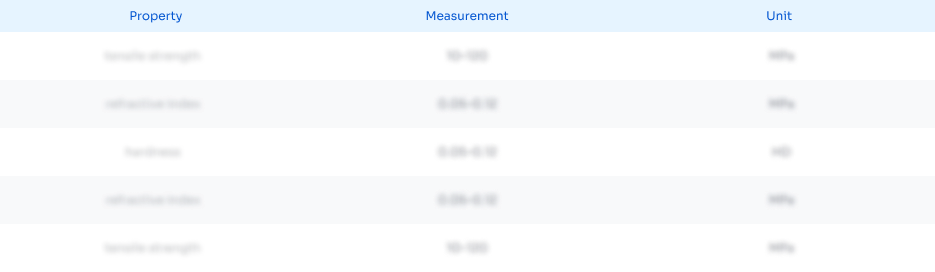
Abstract
Description
Claims
Application Information

- R&D
- Intellectual Property
- Life Sciences
- Materials
- Tech Scout
- Unparalleled Data Quality
- Higher Quality Content
- 60% Fewer Hallucinations
Browse by: Latest US Patents, China's latest patents, Technical Efficacy Thesaurus, Application Domain, Technology Topic, Popular Technical Reports.
© 2025 PatSnap. All rights reserved.Legal|Privacy policy|Modern Slavery Act Transparency Statement|Sitemap|About US| Contact US: help@patsnap.com