Rotary mechanical hand for machining
A mechanical processing and rotary technology, applied in the field of manipulators, can solve problems affecting life and cost control, short life of pressure sensors, and installation errors of grippers, etc., to improve gripping ability and gripping stability, and improve gripping efficiency , the effect of improving the accuracy
- Summary
- Abstract
- Description
- Claims
- Application Information
AI Technical Summary
Problems solved by technology
Method used
Image
Examples
Embodiment Construction
[0030] see Figure 2-5 , in an embodiment of the present invention, a rotary manipulator for mechanical processing, including a mechanical arm mechanism and a grasping mechanical claw 11, wherein three sets of circular arrays of the grasping mechanical claws 11 are installed and connected to the connecting plate 12 , the connecting plate is fixedly installed on the output end of the mechanical arm mechanism; each group of grabbing mechanical claws 11 is driven by a separate cylinder 17, so that the clamping jaws 15 of each grabbing mechanical claw 11 can be realized by the cylinder. action; it is characterized in that an angle detection assembly 20 is provided at the hinge of the end of the clamping jaw away from the clamping end, and the angle detection assembly 20 can detect the rotation angle of the clamping jaw at all times; A controller connected to the detection assembly 20, the controller independently controls each cylinder;
[0031] When grabbing the workpiece 25, th...
PUM
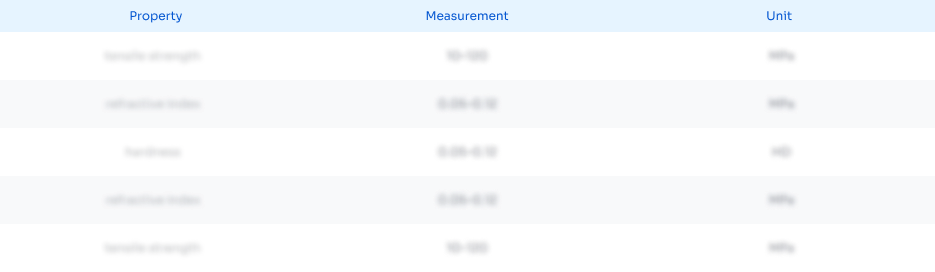
Abstract
Description
Claims
Application Information

- R&D
- Intellectual Property
- Life Sciences
- Materials
- Tech Scout
- Unparalleled Data Quality
- Higher Quality Content
- 60% Fewer Hallucinations
Browse by: Latest US Patents, China's latest patents, Technical Efficacy Thesaurus, Application Domain, Technology Topic, Popular Technical Reports.
© 2025 PatSnap. All rights reserved.Legal|Privacy policy|Modern Slavery Act Transparency Statement|Sitemap|About US| Contact US: help@patsnap.com