Morphology Prediction Method of Metal Cutting Tool Nose Dead Zone Considering Metal Slip
A technology of metal cutting and metal sliding, applied in geometric CAD and other directions
- Summary
- Abstract
- Description
- Claims
- Application Information
AI Technical Summary
Problems solved by technology
Method used
Image
Examples
Embodiment 1
[0097] The finite element simulation is set to a two-dimensional right-angle cutting simulation model of aluminum alloy 7050-T7451, and the tool is set to the radius r of the blunt circle of the tool tip e = 0.02 mm, rake angle α = 5 degrees. The friction coefficient between the blunt circle of the tool nose and the rake face is determined by the cutting data published in the right-angle cutting parameter library. The modeling method of the model refers to the finite element modeling method disclosed in the literature "X.Jin, Y.Altintas, Prediction of micro-milling forces with finite element method, Journal of Materials Processing Technology 212(3)(2012)542-552." .
[0098] Step 1. Set the distance from an unknown point on the blunt circle of the knife tip to the lowest point of the blunt circle as h s . The rake angle α at the unknown point on the blunt circle of the tool tip s Expressed as:
[0099]
[0100] The shear angle φ s Expressed as:
[0101] φ s =45°-(β ...
PUM
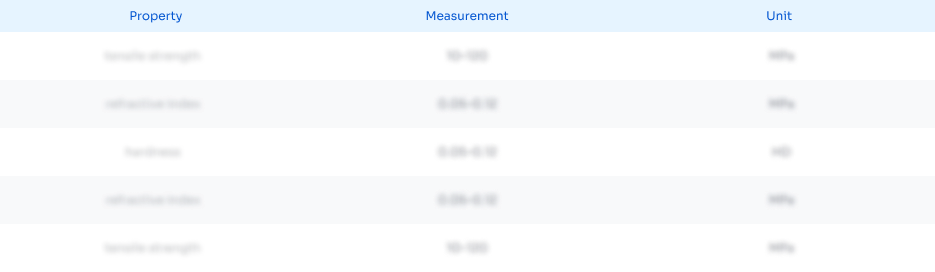
Abstract
Description
Claims
Application Information

- Generate Ideas
- Intellectual Property
- Life Sciences
- Materials
- Tech Scout
- Unparalleled Data Quality
- Higher Quality Content
- 60% Fewer Hallucinations
Browse by: Latest US Patents, China's latest patents, Technical Efficacy Thesaurus, Application Domain, Technology Topic, Popular Technical Reports.
© 2025 PatSnap. All rights reserved.Legal|Privacy policy|Modern Slavery Act Transparency Statement|Sitemap|About US| Contact US: help@patsnap.com