A multi-layer hot water storage tank, a thermal energy recovery and reuse system and a reuse method thereof
A technology for hot water storage tanks and heat energy recovery, which is applied in solar heating systems, solar thermal energy, and non-combustion exothermic chemical reactions to generate heat. It can solve the impact of ammonia recovery efficiency, failure to achieve temperature control, and affect product quality. and other issues to achieve the effect of reducing energy consumption, reducing energy consumption, and reducing production energy consumption
- Summary
- Abstract
- Description
- Claims
- Application Information
AI Technical Summary
Problems solved by technology
Method used
Image
Examples
Embodiment 1
[0096] Heating is an indispensable process in chemical plants and traditional Chinese medicine plants. In the prior art, most of the reaction kettles are heated by stirring jacketed steam. The transfer of heat from the kettle wall to the reaction solution is contact transfer, while the inside of the reaction solution is agitation transfer. In fact, due to heat transfer, the temperature of the reaction solution on the wall of the kettle and the intermediate reaction solution may have a difference of 7-8 °C. And it is often much higher at the upper edge of the reaction liquid, which is because the temperature of the steam is too high, so that the local temperature of the kettle wall is too high. Such uneven temperature often has adverse effects on the reaction, and the quality and yield of the product are reduced. However, the aforementioned problems can be avoided by using the solution provided by the present invention. The system and method of the present invention can be app...
Embodiment 2
[0100]Concentration of aqueous solutions in traditional Chinese medicine factories and chemical factories is the most commonly used process, such as multiple effect evaporators. However, some chemical components are thermally unstable, so it is not suitable to be heated at high temperature for a long time. It is difficult to control the temperature of heating with pressure steam, and the product quality cannot be guaranteed. Adopt recovery system of the present invention, can solve this problem. If these components can withstand 65°C, vacuum distillation can be used. Since the boiling point of water at 25kPa is 65°C, the general steaming process can use a WLW-50 vacuum pump to pump the vacuum below 25kPa and choose suitable hot water. Just be heated to more than 65 ℃, and the water that comes out passes into collection water tank 11. This eliminates the need for pressurized steam. If the chemical composition has a lower temperature resistance, it can be concentrated as long ...
Embodiment 3
[0102] Extraction is a common purification process in chemical and pharmaceutical factories. Organic solvents in extraction include: halogenated hydrocarbons such as chloroform, dichloromethane, etc., aromatic hydrocarbons such as benzene, etc., aliphatic hydrocarbons such as kerosene, petroleum ether, etc., esters such as butyl acetate , ethyl acetate, etc. The organic phase after extraction needs to be distilled to remove the solvent, and the distillation process of the solvent with a boiling point lower than 100° C. can use the thermal energy recovery and reuse system and method provided by the present invention. Taking dichloromethane as an example, dichloromethane should be distilled off after extraction. The boiling point is 39.75°C. Distillation can be heated with water at 50-60°C. Use the water of higher temperature instead, as, the hot water that flows out with intermediate tank 2.
[0103] Water exiting the jacket in the endothermic process plant 12 can be returned ...
PUM
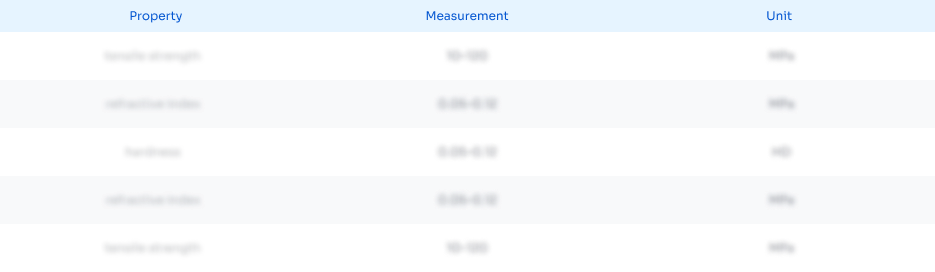
Abstract
Description
Claims
Application Information

- Generate Ideas
- Intellectual Property
- Life Sciences
- Materials
- Tech Scout
- Unparalleled Data Quality
- Higher Quality Content
- 60% Fewer Hallucinations
Browse by: Latest US Patents, China's latest patents, Technical Efficacy Thesaurus, Application Domain, Technology Topic, Popular Technical Reports.
© 2025 PatSnap. All rights reserved.Legal|Privacy policy|Modern Slavery Act Transparency Statement|Sitemap|About US| Contact US: help@patsnap.com