Composite fabric edge closing process
A process and fabric technology, which is applied in the field of composite fabric edge finishing technology, can solve the problems of easy wool adjustment, poor skin-adhesion, and yarn take-off, etc., and achieve the effect of reasonable design, good use effect, beautiful and comfortable appearance
- Summary
- Abstract
- Description
- Claims
- Application Information
AI Technical Summary
Problems solved by technology
Method used
Image
Examples
Embodiment 1
[0028] A composite fabric trimming process, the specific steps are as follows:
[0029] Step 1: When the clothing 5 adopts the double-sided laminated OK black cloth with a thickness of 3.5mm, a mold with forming and cutting functions is made according to the required shape. The mold includes the mold body 1 and the cutting edge 2, surrounded by the cutting edge 2 Mold body 1, cutting edge 2 is provided with a knife edge, the angle of the main cutting edge 3 is 32 degrees, the angle of the negative cutting edge 4 is 40 degrees, the width of the die line is 0.5mm, and the height from the negative cutting edge 4 is 0.6 mm;
[0030] Step 2: Heat the mold to 148 degrees Celsius to melt 5 sides of the garment;
[0031] Step 3: The setting time is 29 seconds and the pressure is 1.4 tons;
[0032] Step 4: Cool the formed garment 5 naturally.
Embodiment 2
[0034] A composite fabric trimming process, the specific steps are as follows:
[0035] Step 1: When the clothing 5 adopts the double-sided laminated OK black cloth with a thickness of 8.1mm, a mold with forming and cutting functions is made according to the required shape. The mold includes the mold body 1 and the cutting edge 2, surrounded by the cutting edge 2 Mold body 1, cutting edge 2 is provided with a knife edge, the angle of the main edge 3 is 35 degrees, the angle of the negative edge 4 is 40 degrees, the width of the die line is 0.65mm, and the height from the negative edge 4 is 1.1 mm;
[0036] Step 2: Heat the mold to 155 degrees Celsius to melt 5 sides of the garment;
[0037] Step 3: The setting time is 38 seconds and the pressure is 3 tons;
[0038] Step 4: Cool the formed garment 5 naturally.
Embodiment 3
[0040] A composite fabric trimming process, the specific steps are as follows:
[0041] Step 1: When the apparel 5 uses EVA composite cloth with a thickness of 5.2mm, a mold with a forming and cutting function is made according to the required shape. The mold includes a mold body 1 and a cutting edge 2. The cutting edge 2 surrounds the mold body 1, and the cutting knife The edge 2 is provided with a knife edge, the angle of the main edge 3 is 25 degrees, the angle of the negative edge 4 is 45 degrees, the width of the die line is 0.5mm, and the height from the negative edge 4 is 0.75mm;
[0042] Step two, heating the mold to 116 degrees Celsius for 60 seconds to melt 5 sides of the garment;
[0043] Step 3: The setting time is 33 seconds and the pressure is 27 tons;
[0044] Step 4: Cool the formed garment 5 naturally.
PUM
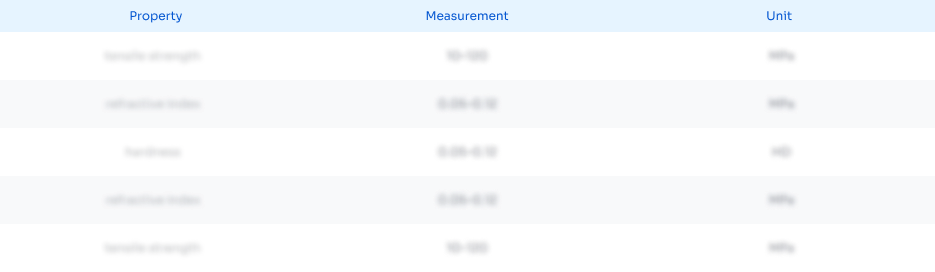
Abstract
Description
Claims
Application Information

- R&D Engineer
- R&D Manager
- IP Professional
- Industry Leading Data Capabilities
- Powerful AI technology
- Patent DNA Extraction
Browse by: Latest US Patents, China's latest patents, Technical Efficacy Thesaurus, Application Domain, Technology Topic, Popular Technical Reports.
© 2024 PatSnap. All rights reserved.Legal|Privacy policy|Modern Slavery Act Transparency Statement|Sitemap|About US| Contact US: help@patsnap.com