Robot control method, controller and system based on layered thread framework
A control method and robot technology, applied in the direction of program-controlled manipulators, comprehensive factory control, manipulators, etc., can solve the problems of long training time and high cost, and achieve the effects of improving training efficiency, reducing workload, and good robustness
- Summary
- Abstract
- Description
- Claims
- Application Information
AI Technical Summary
Problems solved by technology
Method used
Image
Examples
Embodiment 1
[0038] The scene of the robot control method based on the layered thread framework of this embodiment also includes a vision system and a robot motion control system, wherein both the vision system and the robot motion control system are existing structures.
[0039] For example: the vision system can be implemented with industrial cameras;
[0040] The robot motion control system includes the driving device, the mechanical arm, the industrial computer and the workbench.
[0041] The scenario of this embodiment is as figure 1 As shown, the process of realizing the assembly operation is as follows figure 2 As shown, the industrial camera guides the manipulator to the initial position specified in the assembly experiment, and then the manipulator performs the assembly operation, stores the experience pool samples, and then trains the network parameters, and uses the action output by the network as the input of the control system to adjust the movement of the manipulator, there...
Embodiment 2
[0063] like Figure 5 As shown, a robot controller based on a layered thread framework of the present embodiment includes:
[0064] (1) Assembly initial position determination module, which is used to determine the target workpiece pose, and guide the mechanical arm to move directly above the workpiece as the initial assembly position;
[0065] (2) Assembly task decomposition module, which is used to call the assembly task to be completed in the task layer, and then determine the corresponding skill in the skill layer associated with the assembly task and the assembly state parameter in the primitive language layer associated with the corresponding skill;
[0066] (3) a network initialization module, which is used to declare the main network and multiple threads and initialize network parameters; threads include acquisition threads and training threads; the number of training threads is equal to the number of skills associated with the assembly task;
[0067] The main network...
Embodiment 3
[0078] A robot control system based on a layered thread framework, including the above Figure 5 The robot controller based on the hierarchical threading framework is shown.
[0079] In this embodiment, assembly tasks, skills, and assembly states are stored hierarchically in the task layer, skill layer, and primitive layer, and the main network and multiple threads are declared, and the threads include acquisition threads and training threads; the number of training threads is related to the assembly The number of skills associated with tasks is equal; multiple threads do not interfere with each other, which can improve update convergence and reduce correlation compared with previous networks.
[0080] In this embodiment, a collection sample thread and multiple training threads are set up, which improves the training efficiency and reduces the total training time.
[0081] This embodiment takes robot skill learning into consideration, and is suitable for small-batch and multi...
PUM
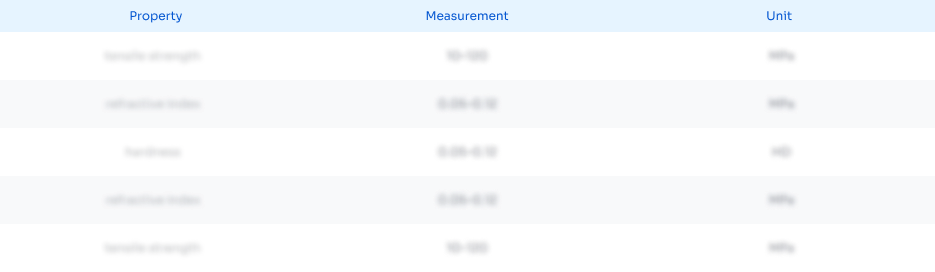
Abstract
Description
Claims
Application Information

- R&D
- Intellectual Property
- Life Sciences
- Materials
- Tech Scout
- Unparalleled Data Quality
- Higher Quality Content
- 60% Fewer Hallucinations
Browse by: Latest US Patents, China's latest patents, Technical Efficacy Thesaurus, Application Domain, Technology Topic, Popular Technical Reports.
© 2025 PatSnap. All rights reserved.Legal|Privacy policy|Modern Slavery Act Transparency Statement|Sitemap|About US| Contact US: help@patsnap.com