Forging piston four-station drilling clamp and machining method
A drilling jig and four-station technology, which is applied in the direction of manufacturing tools, metal processing equipment, metal processing machinery parts, etc., can solve the problems of low production efficiency and difficulty in batch production, and achieve high processing efficiency, high space utilization rate, The effect of improving processing efficiency
- Summary
- Abstract
- Description
- Claims
- Application Information
AI Technical Summary
Problems solved by technology
Method used
Image
Examples
Embodiment 1
[0027] see Figure 1-2 , a forging piston four-station drilling fixture, including a rotary table and a backing plate 2, four precision centering vises 3 are fixedly arranged on the upper surface of the backing plate 2, and four precision centering vises 3 are fixed on the backing plate The upper surface of 2 is arranged in a line and aligned in the X direction. The center distances of the left one and left three precision centering vises 3, the left two and left four precision centering vises 3 are all consistent with the center distances of the double spindles of the machining center. The two ends of the upper surface of each precision centering vise 3 are symmetrically fixed with two claws 5, and the upper part of the claws 5 is equipped with an elastic plunger 6 that protrudes on both sides to tighten the workpiece, and the elastic plunger 6 is set. It is convenient to fix the workpiece, making the fixation convenient and quick. The top of the claw 5 is welded and fixed ...
Embodiment 2
[0030] On the basis of Embodiment 1, the index plate 9 and the tailstock 10 are respectively fixed on the base base 12 through the riser block 11 , thereby maintaining the integrity of the whole device.
[0031] Working principle and processing method of the present invention:
[0032] Assembly: Assemble the special fixtures and tools of the type required for this processing, and calibrate the accuracy of the clamping position, and the double-spindle machine tool is ready to start;
[0033] Feeding: Put the four piston workpieces into the jaws 5 of the special fixture in turn by manual or mechanical hands, and the elastic plunger 6 on the upper part of the jaws 5 is automatically tightened, and the jaws 5 and elastic plunger 6 are waiting for the inside of the hole to be drilled. Peripheral positioning, the support column 7 on the top of the jaw 5 is positioned on the inner top surface of the workpiece;
[0034] Clamping: After the workpiece is placed, the two oil cylinders 1...
PUM
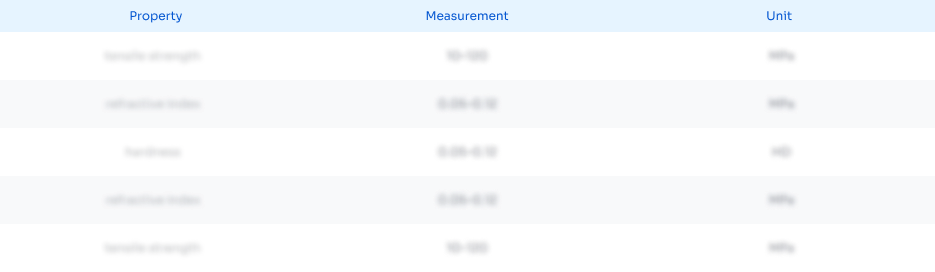
Abstract
Description
Claims
Application Information

- Generate Ideas
- Intellectual Property
- Life Sciences
- Materials
- Tech Scout
- Unparalleled Data Quality
- Higher Quality Content
- 60% Fewer Hallucinations
Browse by: Latest US Patents, China's latest patents, Technical Efficacy Thesaurus, Application Domain, Technology Topic, Popular Technical Reports.
© 2025 PatSnap. All rights reserved.Legal|Privacy policy|Modern Slavery Act Transparency Statement|Sitemap|About US| Contact US: help@patsnap.com