Method for reducing electric leakage of formed aluminum foil
A technology of forming aluminum foil and aluminum foil, which is applied in circuits, capacitors, electrolytic coatings, etc., can solve the problems of stable performance of hydrated alumina film, and achieve the effects of easy industrial production, simple process control, and improved quality
- Summary
- Abstract
- Description
- Claims
- Application Information
AI Technical Summary
Problems solved by technology
Method used
Image
Examples
Embodiment 1
[0041] A kind of concrete operation of the present invention is as follows:
[0042] Take corroded aluminum foil raw materials, in which the Al purity is ≥99.99%, add 1g / L mannitol to water to make a water-mannitol solution, boil the corroded aluminum foil in the water-mannitol solution at 80°C for 10 minutes, and heat it at 60°C At a certain temperature, the aluminum foil is sequentially subjected to primary formation, secondary formation, tertiary formation, fourth-level formation, fifth-level formation, roasting treatment, intermediate treatment, cleaning, post-treatment, drying and other processes.
[0043] The leakage test was carried out on the obtained formed foil. The instrument used in the test was a TV1000 aluminum foil electrical performance tester. The results are shown in figure 2 , after 1200s leakage test, the leakage current is about 68μA.
Embodiment 2
[0045] Another specific operation of the present invention is as follows:
[0046] Take corroded aluminum foil raw materials, in which the Al purity is ≥99.99%, add 6g / L mannitol to water to make a water-mannitol solution, boil the corroded aluminum foil in the water-mannitol solution at 90°C for 10 minutes, and heat it at 85°C At a certain temperature, the aluminum foil is sequentially subjected to primary formation, secondary formation, tertiary formation, fourth-level formation, fifth-level formation, roasting treatment, intermediate treatment, cleaning, post-treatment, drying and other processes.
[0047] The leakage test was carried out on the obtained formed foil. The instrument used in the test was a TV1000 aluminum foil electrical performance tester. The results are shown in image 3 , after 1200s leakage test, the leakage current is about 65μA.
Embodiment 3
[0049] Another specific operation of the present invention is as follows:
[0050]Take corroded aluminum foil raw materials, in which the Al purity is ≥99.99%, add 12g / L mannitol to water to make a water-mannitol solution, boil the corroded aluminum foil in the water-mannitol solution at 100°C for 10 minutes, and then heat it at 100°C At a certain temperature, the aluminum foil is sequentially subjected to primary formation, secondary formation, tertiary formation, fourth-level formation, fifth-level formation, roasting treatment, intermediate treatment, cleaning, post-treatment, drying and other processes.
[0051] The leakage test was carried out on the obtained formed foil. The instrument used in the test was a TV1000 aluminum foil electrical performance tester. The results are shown in Figure 4 , After 1200s leakage test, the leakage current is about 70μA.
PUM
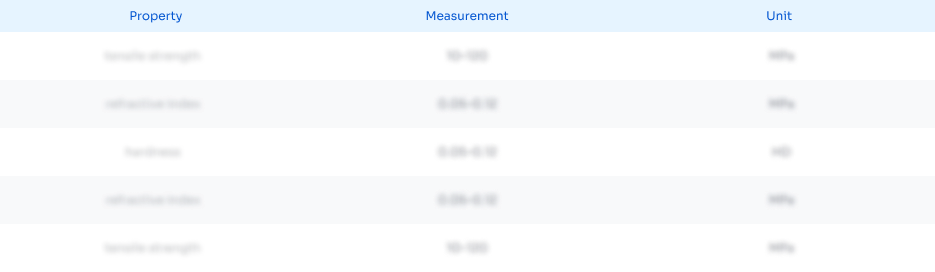
Abstract
Description
Claims
Application Information

- R&D
- Intellectual Property
- Life Sciences
- Materials
- Tech Scout
- Unparalleled Data Quality
- Higher Quality Content
- 60% Fewer Hallucinations
Browse by: Latest US Patents, China's latest patents, Technical Efficacy Thesaurus, Application Domain, Technology Topic, Popular Technical Reports.
© 2025 PatSnap. All rights reserved.Legal|Privacy policy|Modern Slavery Act Transparency Statement|Sitemap|About US| Contact US: help@patsnap.com