A steel-wood hybrid connection structure
A mixed connection, steel-wood technology, applied in building construction, construction, etc., can solve the problems of low shear stiffness of self-tapping screws, failure to meet the requirements of bearing capacity, and screws are easy to be pulled out, etc., to expand the stress-bearing area of wood , Convenience in construction, Improve the effect of shear bearing capacity
- Summary
- Abstract
- Description
- Claims
- Application Information
AI Technical Summary
Problems solved by technology
Method used
Image
Examples
Embodiment 1
[0029] Such as Figure 1~2 , a cylindrical slot 11 is reserved on the upper surface of the plank 1, the depth of the slot 11 is 0.5 times the thickness of the plank 1, the steel member 2 is H-shaped steel, a long slot-shaped reserved hole 21 is reserved on the flange, and self-tapping screws 3 and the flange of the steel member 2 are screwed obliquely at a staggered angle, and arranged symmetrically and staggered on both sides of the symmetry axis of the section of the steel member 2. After the self-tapping screw 3 is installed, pour mortar into the slot 11 of the wooden board 1 4 and smooth.
Embodiment 2
[0031] Such as image 3 , a cylindrical slot 11 is reserved on the upper surface of the plank 1, the depth of the slot 11 is 0.5 times the thickness of the plank 1, the steel member 2 is H-shaped steel, a long slot-shaped reserved hole 21 is reserved on the flange, and self-tapping screws 3 and the flange of the steel member 2 are screwed obliquely at a staggered angle, and are arranged symmetrically and staggered on both sides of the symmetry axis of the steel member 2 section. The tails of each two self-tapping screws 3 are located in the same reserved hole 21 of the wooden board 1, and After the self-tapping screw 3 was installed, pour mortar 4 into the slotted hole 11 of the plank 1 and smooth it out. Such as Figure 4 , the oblique side of the inclined washer 5 is closely attached to the inner surface of the flange of the steel member 2, and the other side is closely attached to the inner surface of the head of the self-tapping screw 3.
Embodiment 3
[0033] Such as Figure 5 , the upper surface of the plank 1 is reserved with a long groove-shaped slot 11, the depth of the slot 11 is 0.5 times the thickness of the plank 1, the steel member 2 is a rectangular tube with a welded flange, and a long groove-shaped reserved hole 21 is reserved on the flange , the self-tapping screws 3 are screwed in obliquely to the flange of the steel member 2, and are arranged symmetrically on both sides of the symmetry axis of the cross-section of the steel member 2. Mortar 4 and smooth.
PUM
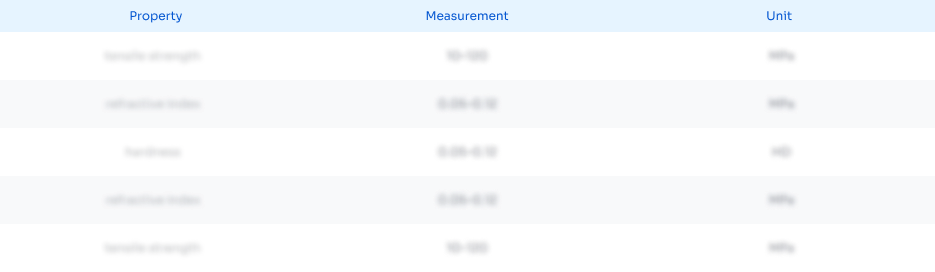
Abstract
Description
Claims
Application Information

- R&D
- Intellectual Property
- Life Sciences
- Materials
- Tech Scout
- Unparalleled Data Quality
- Higher Quality Content
- 60% Fewer Hallucinations
Browse by: Latest US Patents, China's latest patents, Technical Efficacy Thesaurus, Application Domain, Technology Topic, Popular Technical Reports.
© 2025 PatSnap. All rights reserved.Legal|Privacy policy|Modern Slavery Act Transparency Statement|Sitemap|About US| Contact US: help@patsnap.com