Steel wire quenching process
A technology of steel wire and process, applied in the field of steel wire quenching process, can solve the problems of uneven heating of steel wire, large difference in performance of steel wire, low cooling efficiency, etc., to increase cooling and utilization efficiency, increase quenching area, and increase quenching efficiency. The effect of efficiency
- Summary
- Abstract
- Description
- Claims
- Application Information
AI Technical Summary
Problems solved by technology
Method used
Image
Examples
Embodiment Construction
[0029] use Figure 1-Figure 5 A steel wire quenching process according to an embodiment of the present invention is described as follows.
[0030] Such as Figure 1-Figure 5 Shown, a kind of steel wire quenching process of the present invention, this process comprises the following steps;
[0031] S1: Cutting: The steel wire is fed into the cutting machine by feeding the steel wire to cut into uniform steel wire segments;
[0032] S2: Feeding: Send the steel wire segment cut into uniformity into the feeding device 4 provided on the quenching box 1 through the feeding replacement device 3;
[0033] S3: Quenching: The steel wire section is transported to the quenching bin 11 set in the quenching box 1 through the conveyor belt 42 and the elastic fastening belt 44 of the feeding device 4 for quenching, and then the quenching bin 11 is heated to 830°C-870°C and Keep it for 0.5-2.5 hours, cook the steel wire in the whole furnace, and the time for taking out the furnace is 0.3-0....
PUM
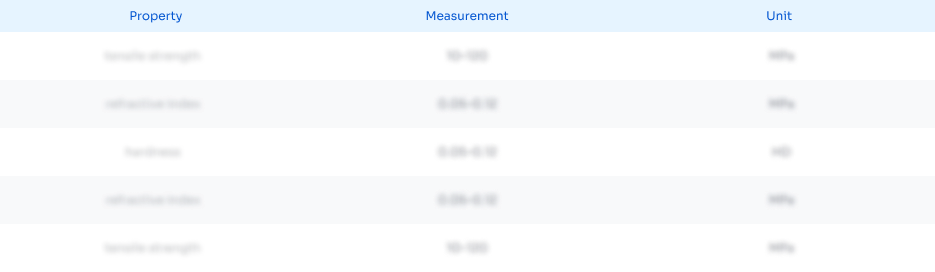
Abstract
Description
Claims
Application Information

- R&D
- Intellectual Property
- Life Sciences
- Materials
- Tech Scout
- Unparalleled Data Quality
- Higher Quality Content
- 60% Fewer Hallucinations
Browse by: Latest US Patents, China's latest patents, Technical Efficacy Thesaurus, Application Domain, Technology Topic, Popular Technical Reports.
© 2025 PatSnap. All rights reserved.Legal|Privacy policy|Modern Slavery Act Transparency Statement|Sitemap|About US| Contact US: help@patsnap.com