System and method for following industrial vehicle
An industrial vehicle and vehicle technology, which is applied to vehicle components, transportation and packaging, and external condition input parameters, etc., can solve problems such as difficult to achieve high-precision positioning effects, high requirements for the surrounding environment, and complex algorithm systems, etc., to provide work Efficiency, fast data propagation rate, high time resolution effect
- Summary
- Abstract
- Description
- Claims
- Application Information
AI Technical Summary
Problems solved by technology
Method used
Image
Examples
Embodiment Construction
[0046] The present invention will be further described below through specific embodiments.
[0047] The vehicle control system usually includes a brake control module 10, a travel / lift control module, a steering control module, and so on. The driving / lifting control module is provided with a driving / lifting controller 12, a driving motor 14 and a hoisting motor 13, and the driving / lifting controller 12 is used to control the driving motor 14 and the hoisting motor 13. The brake control module 10 is used to realize the brake control of the traveling motor 14. The steering control module is provided with a steering controller 11 and a steering motor 15, and the steering motor 15 is controlled by the steering controller 11 to realize steering control. In the manual driving mode, the driver can manually control the forklift's driving, steering, and lifting functions through routine operations of the vehicle.
[0048] Reference Figure 1 to Figure 10 , The following system of an indus...
PUM
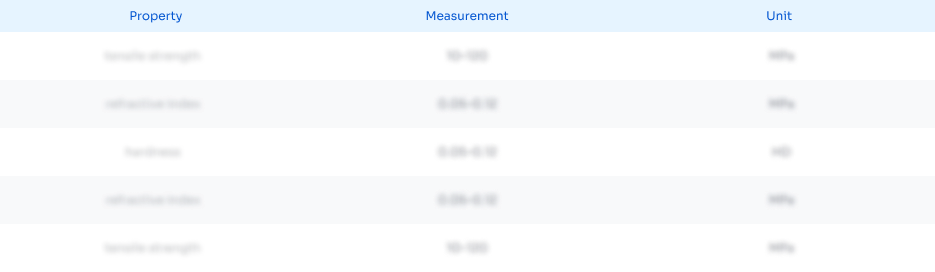
Abstract
Description
Claims
Application Information

- R&D
- Intellectual Property
- Life Sciences
- Materials
- Tech Scout
- Unparalleled Data Quality
- Higher Quality Content
- 60% Fewer Hallucinations
Browse by: Latest US Patents, China's latest patents, Technical Efficacy Thesaurus, Application Domain, Technology Topic, Popular Technical Reports.
© 2025 PatSnap. All rights reserved.Legal|Privacy policy|Modern Slavery Act Transparency Statement|Sitemap|About US| Contact US: help@patsnap.com