A micro-positioning device based on normal stress electromagnetic drive
An electromagnetic drive and normal stress technology, applied in the direction of electromechanical devices, electric components, electrical components, etc., can solve the problems that the micro-scanning platform cannot meet the rigid requirements and large output, and achieve large output force, assembly-free, and simple structure compact effect
- Summary
- Abstract
- Description
- Claims
- Application Information
AI Technical Summary
Problems solved by technology
Method used
Image
Examples
Embodiment Construction
[0030] The present invention will be further described below in conjunction with the accompanying drawings and specific embodiments.
[0031] Such as Figure 1 to Figure 4 As shown, the micro-positioning device based on normal stress electromagnetic drive in this embodiment includes a base 1, a mover ring 2, a flexible transmission assembly 3 and multiple sets of linear normal stress electromagnetic actuators 4, and the middle part of the base 1 is provided with Installation cavity 101, mover ring 2 is installed in the installation cavity 101 through flexible transmission assembly 3, wherein the mover ring 2 is used to install optical lenses; multiple sets of linear normal stress electromagnetic actuators 4 are installed in the mover ring in a ring shape 2 on the base 1 on the peripheral side; each linear normal stress electromagnetic actuator 4 includes a stator yoke 401 and a coil winding 402 wound on the stator yoke 401; the peripheral side of the mover ring 2 is provided w...
PUM
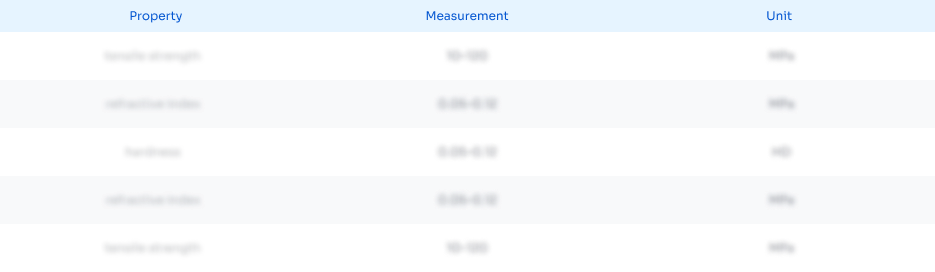
Abstract
Description
Claims
Application Information

- R&D
- Intellectual Property
- Life Sciences
- Materials
- Tech Scout
- Unparalleled Data Quality
- Higher Quality Content
- 60% Fewer Hallucinations
Browse by: Latest US Patents, China's latest patents, Technical Efficacy Thesaurus, Application Domain, Technology Topic, Popular Technical Reports.
© 2025 PatSnap. All rights reserved.Legal|Privacy policy|Modern Slavery Act Transparency Statement|Sitemap|About US| Contact US: help@patsnap.com