Core tube valve capable of achievingautomatic cutting duringbothway pipeline burst
A pipeline and core tube technology, which is applied in the sub-series of the conventional core tube valve plate, in the field of two-way pipeline burst self-cutting core tube valves, can solve the problems of uncontrollable resources, casualties, economic losses, pipeline resource loss and environmental damage, etc., to achieve Resource and life safety protection, improved reliability and safety, good inner sealing effect
- Summary
- Abstract
- Description
- Claims
- Application Information
AI Technical Summary
Problems solved by technology
Method used
Image
Examples
Embodiment 1
[0036] See attached figure 1 , 2 , 3, the two-way pipeline burst self-operated cut-off core tube valve described in this embodiment; the valve core tube 1 is the sleeve tube I2' that runs through the valve body 2 in the same axial direction as the fixing piece, the inner cavity 200 of the valve body 2, and the valve body 2’s sleeve pipe II 2″; there is an axial partition 100 in the middle of the spool tube 1, the interlayer 100 is composed of the inner core and the middle section of the spool tube 1 radially radiating from the inner core, and the two axial end faces of the inner core of the interlayer 100 are tongues triangular slope surface 100′; the axially adjacent two sides of the interlayer 100 are respectively two radial flow holes 103 of the input section 1′ and the output section 1″; ' and the annular valve seat 201 at the throat of the sleeve tube II2" all constitute a sealing pair; the input section 1' and the sleeve tube I2' and the output section 1" and the sleeve...
Embodiment 2
[0041] See attached Figure 4 , 5 6. The bidirectional pipe burst self-cutting core tube valve described in the embodiment; the valve core tube 1 is a sleeve tube I2' coaxially penetrating through the valve body 2, the inner cavity 200 of the valve body 2, and the valve body 2. Sleeve II 2″; there is an axial partition 100 in the middle of the valve core tube 1, and the partition 100 is composed of the inner core and the middle section of the core tube 1 radially radiating from the inner core, and the two axial end faces of the core tube 100 are tongue-shaped The triangular slope surface 100'; the axially adjacent two sides of the interlayer 100 are respectively the two radial flow holes 103 of the input section 1' and the output section 1"; the sealing surface of the annular valve core 101 surrounding and embedded in the interlayer 100 is bidirectional The slope surface and the annular valve seat 201 at the throat of the sleeve tube I2' and the sleeve tube II2" all constitut...
Embodiment 3
[0046] See attached Figure 7 , 8 , 9, the two-way pipe burst self-cutting core tube valve described in this embodiment; the valve core tube 1 is a sleeve tube I2' that runs through the valve body 2 in the same axial direction as the fixing piece, the inner cavity 200 of the valve body 2, and the valve body 2’s sleeve tube II 2″; there is an axial partition 100 in the middle of the spool tube 1, the interlayer 100 is composed of the inner core and the middle section of the spool tube 1 radially radiating from the inner core, and the two axial end faces of the inner core of the interlayer 100 are spherical surfaces ; The axially adjacent two sides of the interlayer 100 are respectively the four radial flow holes 103 of the input section 1' and the output section 1 "; The annular valve seat 201 at the top constitutes a sealing pair; bellows seals 300 are provided at the joints of the input section 1' and the sleeve I2' and the output section 1" and the sleeve II2"; a hydraulic ...
PUM
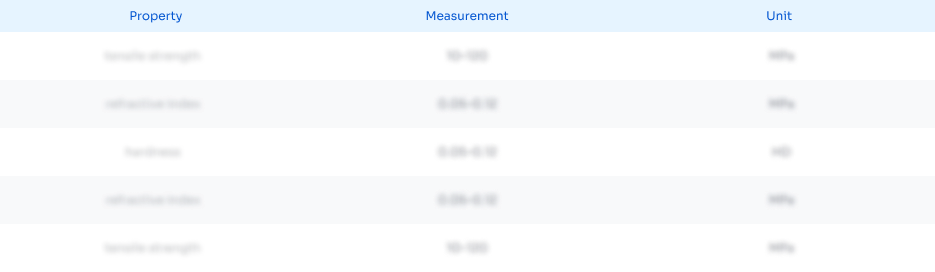
Abstract
Description
Claims
Application Information

- Generate Ideas
- Intellectual Property
- Life Sciences
- Materials
- Tech Scout
- Unparalleled Data Quality
- Higher Quality Content
- 60% Fewer Hallucinations
Browse by: Latest US Patents, China's latest patents, Technical Efficacy Thesaurus, Application Domain, Technology Topic, Popular Technical Reports.
© 2025 PatSnap. All rights reserved.Legal|Privacy policy|Modern Slavery Act Transparency Statement|Sitemap|About US| Contact US: help@patsnap.com