Simulation method for direct coupling of three loads of temperature, pressure and vibration on sensor
A simulation method and sensor technology, applied in the direction of instrumentation, calculation, electrical digital data processing, etc., can solve problems such as difficulty in exporting initial stress files, difficulty in obtaining initial stress files, sensor influence, etc., to overcome conflicts in boundary constraint settings, The maximum response result is accurate and the effect of overcoming stress accumulation
- Summary
- Abstract
- Description
- Claims
- Application Information
AI Technical Summary
Problems solved by technology
Method used
Image
Examples
Embodiment Construction
[0042] The technical solution of the present invention will be described in detail below with reference to the drawings and specific embodiments.
[0043] Such as figure 1 Shown is the overall flow diagram of the simulation method for the direct coupling of temperature, pressure, and vibration on the sensor proposed in the present invention, including the conversion of frequency domain signals to time domain signals, the expansion of time domain signals, the establishment of sensor models based on ANSYSworkbench and Pre-processing, three kinds of environmental load application and coupling simulation condition setting, simulation solution, post-processing and analysis of the results, etc., the coupling simulation of multiple loads is the comprehensive stress simulation, based on the three-load direct coupling simulation method proposed by the present invention The obtained comprehensive stress simulation of the sensor can realize the direct coupling simulation of various environme...
PUM
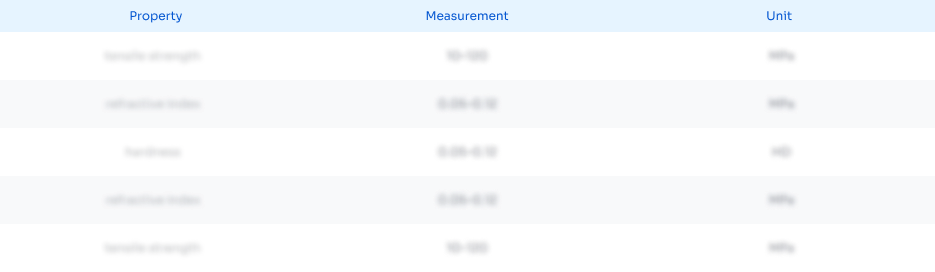
Abstract
Description
Claims
Application Information

- R&D
- Intellectual Property
- Life Sciences
- Materials
- Tech Scout
- Unparalleled Data Quality
- Higher Quality Content
- 60% Fewer Hallucinations
Browse by: Latest US Patents, China's latest patents, Technical Efficacy Thesaurus, Application Domain, Technology Topic, Popular Technical Reports.
© 2025 PatSnap. All rights reserved.Legal|Privacy policy|Modern Slavery Act Transparency Statement|Sitemap|About US| Contact US: help@patsnap.com