Reinforced propeller for unmanned aerial vehicle
An enhanced propeller technology, applied in the field of drones, can solve the problems of low service life of propeller blades, easy breakage of propeller blades, economic losses, etc., and achieve the effect of reducing capital expenditure, reducing experiment cost and reducing waste
- Summary
- Abstract
- Description
- Claims
- Application Information
AI Technical Summary
Problems solved by technology
Method used
Image
Examples
Embodiment Construction
[0025] The technical solutions in the embodiments of the present invention will be clearly and completely described below in conjunction with the accompanying drawings in the embodiments of the present invention. Obviously, the described embodiments are only a part of the embodiments of the present invention, rather than all the embodiments. Based on the embodiments of the present invention, all other embodiments obtained by those of ordinary skill in the art without creative work shall fall within the protection scope of the present invention.
[0026] See Figure 1-Figure 4 A reinforced propeller for unmanned aerial vehicles shown includes an unmanned aerial vehicle motor 1, a connecting hoop 2 is provided on the top of a rotating shaft of the unmanned aerial vehicle motor 1, and a side surface of the connecting hoop 2 is arranged A telescopic rod 3, the left end of the telescopic rod 3 is fixedly connected to the side surface of the connecting hoop 2, a propeller blade 4 is pr...
PUM
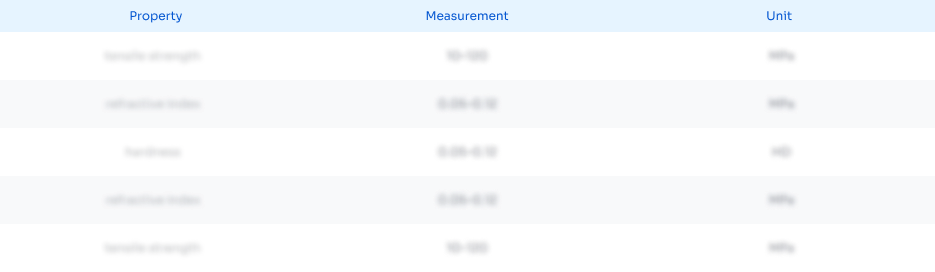
Abstract
Description
Claims
Application Information

- R&D
- Intellectual Property
- Life Sciences
- Materials
- Tech Scout
- Unparalleled Data Quality
- Higher Quality Content
- 60% Fewer Hallucinations
Browse by: Latest US Patents, China's latest patents, Technical Efficacy Thesaurus, Application Domain, Technology Topic, Popular Technical Reports.
© 2025 PatSnap. All rights reserved.Legal|Privacy policy|Modern Slavery Act Transparency Statement|Sitemap|About US| Contact US: help@patsnap.com