A linear-rotational dual-degree-of-freedom oscillating motor and its control method
A technology of oscillating motors and control methods, applied in the direction of electromechanical devices, electrical components, electric components, etc., can solve problems such as low efficiency, high noise, and easy impact on cylinder clearance
- Summary
- Abstract
- Description
- Claims
- Application Information
AI Technical Summary
Problems solved by technology
Method used
Image
Examples
Embodiment Construction
[0033] The present invention will be further described below in conjunction with the accompanying drawings and specific embodiments.
[0034] The following descriptions are only preferred embodiments of the present invention. It should be pointed out that for those skilled in the art, based on the same invention and creation principle of the present invention, several modifications and improvements can also be made, as well as the application of this technical solution in other similar fields, but these all fall within the scope of protection of the present invention. scope.
[0035] See attached Figures 1 to 3 , figure 1 Shown is the overall structure of the present invention, and the labels in the figure are listed as follows: 1-linear-rotational two-degree-of-freedom oscillating motor slave machine cylinder, 2-linear-rotational two-degree-of-freedom oscillating motor slave part air inlet / outlet hole , 3-line-rotation dual-degree-of-freedom oscillating motor follower fix...
PUM
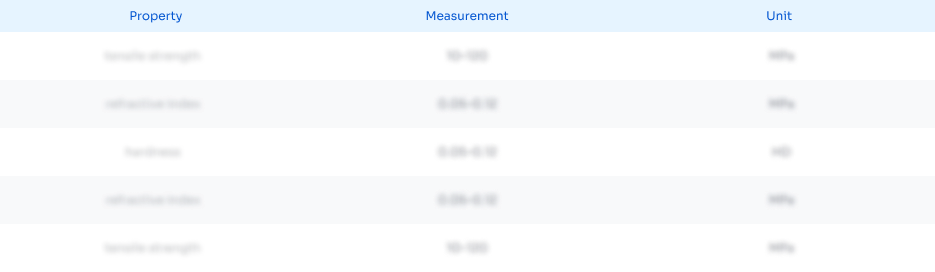
Abstract
Description
Claims
Application Information

- R&D
- Intellectual Property
- Life Sciences
- Materials
- Tech Scout
- Unparalleled Data Quality
- Higher Quality Content
- 60% Fewer Hallucinations
Browse by: Latest US Patents, China's latest patents, Technical Efficacy Thesaurus, Application Domain, Technology Topic, Popular Technical Reports.
© 2025 PatSnap. All rights reserved.Legal|Privacy policy|Modern Slavery Act Transparency Statement|Sitemap|About US| Contact US: help@patsnap.com