Damping system used for mechanical arm tail end detection sensor
A technology of end detection and shock absorption system, which is applied in the direction of manipulators, manufacturing tools, etc., can solve the problems of reduced detection efficiency and long waiting time for vibration elimination, and achieve the effect of improving detection efficiency
- Summary
- Abstract
- Description
- Claims
- Application Information
AI Technical Summary
Problems solved by technology
Method used
Image
Examples
Embodiment 1
[0027] Such as figure 1 As shown, this embodiment provides a shock absorbing system for the detection sensor at the end of the mechanical arm, including an amplitude detection sensor module, a fuzzy control system and a control motor module connected in sequence,
[0028] Amplitude detection sensor module: mounted on the end of the manipulator, used to detect the amplitude value at the end of the manipulator, and transmit the detected amplitude value to the fuzzy control system;
[0029] Fuzzy control system: responsible for fuzzifying the received amplitude value, judging the change of the control motor module according to the pre-established fuzzy rules, and outputting the speed control command to the control motor module;
[0030] Control motor module: adjust its own motion according to the speed control command received.
[0031] The amplitude detection sensing module includes a horizontal laser displacement sensor for detecting the displacement of the end of the mechanic...
PUM
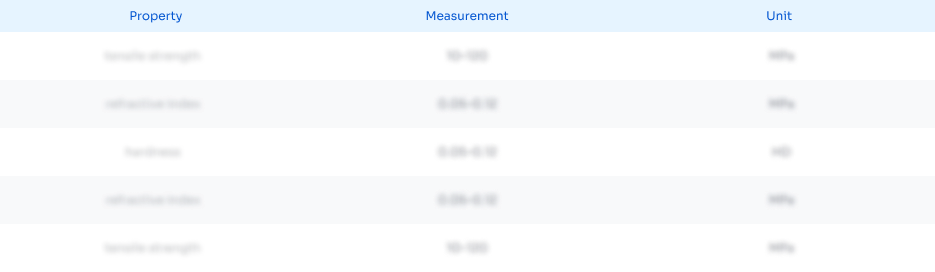
Abstract
Description
Claims
Application Information

- Generate Ideas
- Intellectual Property
- Life Sciences
- Materials
- Tech Scout
- Unparalleled Data Quality
- Higher Quality Content
- 60% Fewer Hallucinations
Browse by: Latest US Patents, China's latest patents, Technical Efficacy Thesaurus, Application Domain, Technology Topic, Popular Technical Reports.
© 2025 PatSnap. All rights reserved.Legal|Privacy policy|Modern Slavery Act Transparency Statement|Sitemap|About US| Contact US: help@patsnap.com