2,3,5,6-tetrachloropyridine synthesis and separation method
A technology of tetrachloropyridine and synthesis method, which is applied in the field of 2,3,5,6-tetrachloropyridine synthesis and separation, can solve the problems of large investment in reaction equipment, high process requirements, increased production cost, etc., and achieves improved electrocatalysis Activity, high product purity, low environmental pollution effect
- Summary
- Abstract
- Description
- Claims
- Application Information
AI Technical Summary
Problems solved by technology
Method used
Image
Examples
Embodiment 1
[0020] A kind of 2,3,5,6-tetrachloropyridine synthetic method, comprises the following operation steps:
[0021] (1) Heat pyridine and chlorine gas to 200°C respectively according to the molar ratio of 2:4, and the vaporized pyridine and chlorine gas are passed into the primary chlorination reactor with an internal temperature of 300°C. After reacting for 50 seconds, the reaction gas All pass into the quenching tower, collect 2-chloropyridine and 2,6-dichloropyridine in the liquid phase in the quenching tower;
[0022] (2) After heating 2-chloropyridine and 2,6-dichloropyridine to 250°C to vaporize, introduce the gas into the intermediate chlorination reactor with an internal temperature of 340°C, and pass excess chlorine gas into it, and stay for 25 seconds to react Finally, the mixed gas is passed into the quench tower to obtain 2,3,6-trichloropyridine and 2,3,5-trichloropyridine in the liquid phase;
[0023] (3) After heating the 2,3,6-trichloropyridine and 2,3,5-trichloro...
Embodiment 2
[0029] A kind of 2,3,5,6-tetrachloropyridine synthetic method, comprises the following operation steps:
[0030] (1) Heat pyridine and chlorine gas to 230°C according to the ratio of molar ratio of 2:6, and the vaporized pyridine and chlorine gas are passed into the primary chlorination reactor with an internal temperature of 350°C. After reacting for 60 seconds, the reaction gas All pass into the quenching tower, collect 2-chloropyridine and 2,6-dichloropyridine in the liquid phase in the quenching tower;
[0031] (2) After heating 2-chloropyridine and 2,6-dichloropyridine to 260°C to vaporize, introduce the gas into the intermediate chlorination reactor with an internal temperature of 380°C, and pass excess chlorine gas into it, and stay for 30 seconds to react Finally, the mixed gas is passed into the quench tower to obtain 2,3,6-trichloropyridine and 2,3,5-trichloropyridine in the liquid phase;
[0032] (3) After heating the 2,3,6-trichloropyridine and 2,3,5-trichloropyri...
PUM
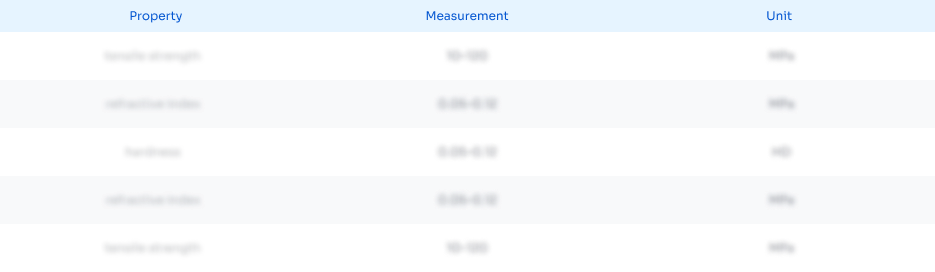
Abstract
Description
Claims
Application Information

- Generate Ideas
- Intellectual Property
- Life Sciences
- Materials
- Tech Scout
- Unparalleled Data Quality
- Higher Quality Content
- 60% Fewer Hallucinations
Browse by: Latest US Patents, China's latest patents, Technical Efficacy Thesaurus, Application Domain, Technology Topic, Popular Technical Reports.
© 2025 PatSnap. All rights reserved.Legal|Privacy policy|Modern Slavery Act Transparency Statement|Sitemap|About US| Contact US: help@patsnap.com