Method for detecting various safety belt electric clearances based on model attributes
An attribute pair, clear distance technology, applied in 3D modeling, electrical digital data processing, CAD numerical modeling, etc., can solve problems such as loss of key information, potential safety hazards, and error-prone
- Summary
- Abstract
- Description
- Claims
- Application Information
AI Technical Summary
Problems solved by technology
Method used
Image
Examples
Embodiment Construction
[0028] The following descriptions are preferred implementation examples of the present invention, which do not limit the protection scope of the present invention.
[0029] like figure 1 As shown, the method for detecting the net distance of various safety belts based on model attributes proposed by the present invention includes the following steps.
[0030] Step 1. Establish a 3D calibration space. Project information needs to be imported, including the 3D models of electrified facilities and 3D models of auxiliary facilities required for the project.
[0031] Establish a three-dimensional verification space, which is essentially a three-dimensional space with three directions, which is used to import the inspection facilities required by the project, such as figure 2 Example diagram of importing 3D calibration space facilities. The imported models are mainly divided into two categories: the 3D model of the charged body facilities required by the project, and the 3D mode...
PUM
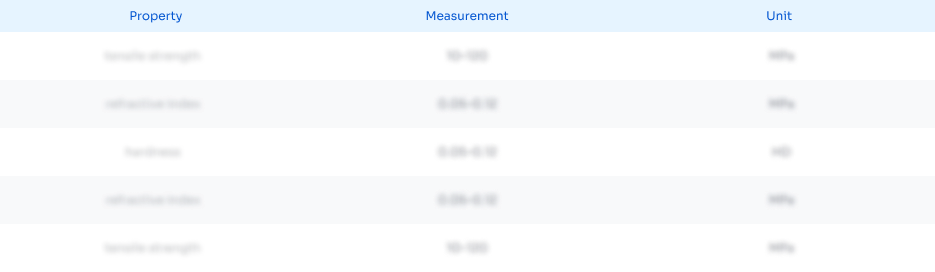
Abstract
Description
Claims
Application Information

- R&D Engineer
- R&D Manager
- IP Professional
- Industry Leading Data Capabilities
- Powerful AI technology
- Patent DNA Extraction
Browse by: Latest US Patents, China's latest patents, Technical Efficacy Thesaurus, Application Domain, Technology Topic, Popular Technical Reports.
© 2024 PatSnap. All rights reserved.Legal|Privacy policy|Modern Slavery Act Transparency Statement|Sitemap|About US| Contact US: help@patsnap.com