Mobile fabricated beam erection system for support method beam splicing of prefabricated segmental beams
A support system and assembly technology, applied in the erection/assembly of bridges, bridges, bridge construction, etc., can solve the problems of low efficiency, high requirements on beam alignment accuracy, and high equipment dependence.
- Summary
- Abstract
- Description
- Claims
- Application Information
AI Technical Summary
Problems solved by technology
Method used
Image
Examples
Embodiment 1
[0041] Example 1, such as Figure 1-4 shown;
[0042] A mobile assembly beam erecting system for prefabricated segmental beam support method, including:
[0043] The gantry crane track foundation 41; the gantry crane track foundation 41 is poured on the ground on both sides of the pier and made, and a gantry crane track (not shown) is installed on each gantry crane track foundation 41;
[0044] Gantry Crane 4; Gantry Crane 4 is removably installed on the Gantry Crane track;
[0045] A spreader 21 for hoisting the beam 2; the spreader 21 is movably installed on the gantry crane 4;
[0046] Support system 3; support system 3 is installed on both sides of the pier;
[0047] Steel rail 5; multiple steel rails 5 are installed on the top of support system 3;
[0048] The sliding wire top 1; the beam 2 is placed on a plurality of sliding wire tops 1, and each sliding wire top 1 slides on a steel rail 5 correspondingly.
[0049] The rated lifting capacity of the gantry crane 4 is...
Embodiment 2
[0052] Example 2, such as Figure 5-11 shown;
[0053] The difference between this embodiment and Embodiment 1 is that the sliding wire top 1 includes:
[0054] The wire head 11; the lower end of the wire head 11 is provided with a spherical groove, and the beam 2 is placed on the top of the wire head 11;
[0055] Chuck 12;
[0056] Screw mandrel 13; the top of screw mandrel 13 is formed as outwardly protruding spherical structure 131, and spherical structure 131 is nested in the spherical groove and is formed as a rotatable movable head; The spherical structure 131 bottom of screw mandrel 13 is formed with Disc notch 132, the chuck 12 is set on the chuck notch 132, the upper end of the chuck 12 is fixedly connected with the bottom of the wire head 11, and the size of the chuck 12 is used to prevent the movable head from disengaging; An adjustment hole 133 for adjusting the horizontal height of the screw mandrel 13 is formed on the screw mandrel 13 below the 132; an outer w...
Embodiment 3
[0074] Example 3, such as Figure 10 shown;
[0075] The difference between this embodiment and Embodiment 2 is that the chuck 12 includes a first sub-chuck 121 and a second sub-chuck 122, the first sub-chuck 121 and the second sub-chuck 122 have the same shape, and the first sub-chuck Both the disk 121 and the second sub-chuck 122 are provided with a semicircular notch 141 on one side, and the side of the first sub-chuck 121 provided with the semicircular notch 141 and the side of the second sub-chuck 122 are provided with a semicircular notch. One side of the notch 141 is butted, and the chuck notch 132 is surrounded in the middle, and the radius of the round hole surrounded by the first sub-chuck 121 and the second sub-chuck 122 is smaller than the radius of the spherical structure 131 and the radius of the spherical groove .
PUM
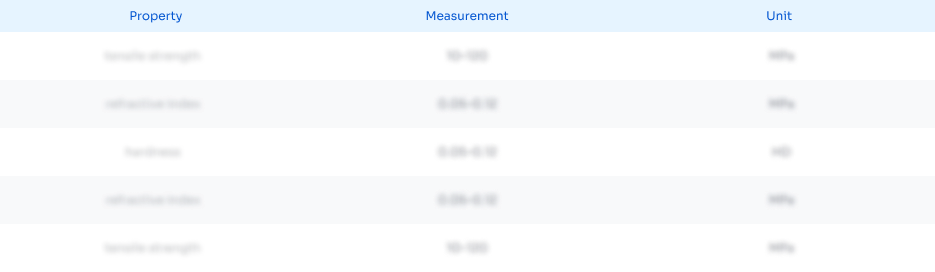
Abstract
Description
Claims
Application Information

- Generate Ideas
- Intellectual Property
- Life Sciences
- Materials
- Tech Scout
- Unparalleled Data Quality
- Higher Quality Content
- 60% Fewer Hallucinations
Browse by: Latest US Patents, China's latest patents, Technical Efficacy Thesaurus, Application Domain, Technology Topic, Popular Technical Reports.
© 2025 PatSnap. All rights reserved.Legal|Privacy policy|Modern Slavery Act Transparency Statement|Sitemap|About US| Contact US: help@patsnap.com