Composite cement-based anti-frosting tile binder
A ceramic tile adhesive and composite cement technology, which is applied in the field of inorganic adhesives, can solve the problems of anti-frosting performance and bond strength that cannot be further improved, and achieve the effects of reducing possibility, content, and porosity
- Summary
- Abstract
- Description
- Claims
- Application Information
AI Technical Summary
Problems solved by technology
Method used
Examples
example 1
[0030] Mix titanium dioxide and potassium carbonate in a grinder at a molar ratio of 4.0:1.5, and mix and grind for 15 hours to obtain a mixed powder. After calcining the mixed powder at a temperature of 850 r / min for 16 hours, a pretreated mixed powder blank is obtained. The pretreated mixed powder blank was washed 8 times with hydrochloric acid with a mass fraction of 15%, and then washed 8 times with deionized water, and the washed pretreated mixed powder blank was dried at a temperature of 90°C for 3 hours to obtain To pretreat the mixed powder, mix the pretreated mixed powder with a silver nitrate solution with a mass fraction of 28% at a mass ratio of 1:12, soak at room temperature for 8 hours, and filter to obtain a modified powder blank. The modified powder blank was placed in After drying for 3 hours at a temperature of 80°C, the modified powder was obtained. Mix the modified powder and graphene oxide at a mass ratio of 2:1, and stir and mix for 50 minutes at a tempera...
example 2
[0032] Mix titanium dioxide and potassium carbonate in a grinder at a molar ratio of 4.0:1.5, and mix and grind for 15 hours to obtain a mixed powder. After calcining the mixed powder at a temperature of 850 r / min for 16 hours, a pretreated mixed powder blank is obtained. The pretreated mixed powder blank was washed 8 times with hydrochloric acid with a mass fraction of 15%, and then washed 8 times with deionized water, and the washed pretreated mixed powder blank was dried at a temperature of 90°C for 3 hours to obtain To pretreat the mixed powder, mix the pretreated mixed powder with a silver nitrate solution with a mass fraction of 28% at a mass ratio of 1:12, soak at room temperature for 8 hours, and filter to obtain a modified powder blank. The modified powder blank was placed in After drying for 3 hours at a temperature of 80°C, the modified powder was obtained. Mix the modified powder and graphene oxide at a mass ratio of 2:1, and stir and mix for 50 minutes at a tempera...
example 3
[0034] Mix titanium dioxide and potassium carbonate in a grinder at a molar ratio of 4.0:1.5, and mix and grind for 15 hours to obtain a mixed powder. After calcining the mixed powder at a temperature of 850 r / min for 16 hours, a pretreated mixed powder blank is obtained. The pretreated mixed powder blank was washed 8 times with hydrochloric acid with a mass fraction of 15%, and then washed 8 times with deionized water, and the washed pretreated mixed powder blank was dried at a temperature of 90°C for 3 hours to obtain To pretreat the mixed powder, mix the pretreated mixed powder with a silver nitrate solution with a mass fraction of 28% at a mass ratio of 1:12, soak at room temperature for 8 hours, and filter to obtain a modified powder blank. The modified powder blank was placed in After drying for 3 hours at a temperature of 80°C, the modified powder was obtained. Mix the modified powder and graphene oxide at a mass ratio of 2:1, and stir and mix for 50 minutes at a tempera...
PUM
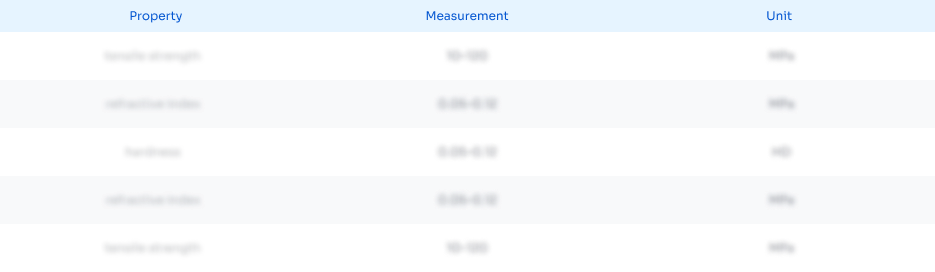
Abstract
Description
Claims
Application Information

- Generate Ideas
- Intellectual Property
- Life Sciences
- Materials
- Tech Scout
- Unparalleled Data Quality
- Higher Quality Content
- 60% Fewer Hallucinations
Browse by: Latest US Patents, China's latest patents, Technical Efficacy Thesaurus, Application Domain, Technology Topic, Popular Technical Reports.
© 2025 PatSnap. All rights reserved.Legal|Privacy policy|Modern Slavery Act Transparency Statement|Sitemap|About US| Contact US: help@patsnap.com