Brake disc shell type lamination casting method and casting mold
A technology of casting molds and brake discs, which is applied in the direction of manufacturing tools, casting molding equipment, casting molds, etc., can solve the problems of huge production line equipment, declining product competitiveness, and insufficient response ability, so as to improve order adaptability and product performance The effect of improving and saving equipment investment costs
- Summary
- Abstract
- Description
- Claims
- Application Information
AI Technical Summary
Problems solved by technology
Method used
Image
Examples
Embodiment Construction
[0026] The specific embodiment of the present invention will be further described in detail below in conjunction with the accompanying drawings.
[0027] It should be noted that, in the following specific embodiments, when describing the embodiments of the present invention in detail, in order to clearly show the structure of the present invention for the convenience of description, the structures in the drawings are not drawn according to the general scale, and are drawn Partial magnification, deformation and simplification are included, therefore, it should be avoided to be interpreted as a limitation of the present invention.
[0028] In the following specific embodiments of the present invention, please refer to Figure 1-Figure 4 , figure 1 It is a structural schematic diagram of a laminated casting mold for a brake disc shell with an air duct.
[0029] The stacked casting method of the brake disc shell with air duct of the present invention is divided into four steps ...
PUM
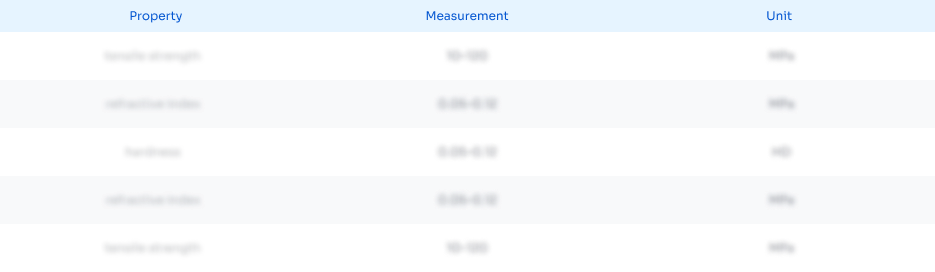
Abstract
Description
Claims
Application Information

- R&D
- Intellectual Property
- Life Sciences
- Materials
- Tech Scout
- Unparalleled Data Quality
- Higher Quality Content
- 60% Fewer Hallucinations
Browse by: Latest US Patents, China's latest patents, Technical Efficacy Thesaurus, Application Domain, Technology Topic, Popular Technical Reports.
© 2025 PatSnap. All rights reserved.Legal|Privacy policy|Modern Slavery Act Transparency Statement|Sitemap|About US| Contact US: help@patsnap.com