Ultrasonic plasticizing micro-injection molding machine main body and molding method
A micro-injection and molding machine technology, applied in the field of advanced molding and manufacturing, can solve the problems of not considering the precise measurement of polymer melt, the large proportion of waste, and the maintenance and replacement of parts without considering the wear condition, so as to reduce the manual feeding time. Effect
- Summary
- Abstract
- Description
- Claims
- Application Information
AI Technical Summary
Problems solved by technology
Method used
Image
Examples
Embodiment Construction
[0065] Such as figure 1 As shown, the main body of the ultrasonic plasticizing micro-injection molding machine disclosed in this embodiment includes a quantitative feeding module 1 , an ultrasonic plasticizing module 2 , a metering module 3 , an injection module 4 and a mold clamping unit 5 .
[0066] Such as figure 2 As shown, the quantitative feeding module 1 includes a translation mechanism 11, a rotation mechanism 12, a feeding pressure assembly 13 and a barrel assembly 14, wherein the translation mechanism 11 is a screw slide table, and the rotation mechanism 12 is connected to the slide table. The feed press assembly 13 is connected with the rotating mechanism 2 , and the bottom end of the feed press assembly passes through the barrel assembly 14 and extends into the plasticizing cavity 22 of the ultrasonic plasticizing module 2 .
[0067] Such as figure 2 As shown, the rotating mechanism 12 includes a motor base 121 and a stepping motor 122. The motor base 121 is a ...
PUM
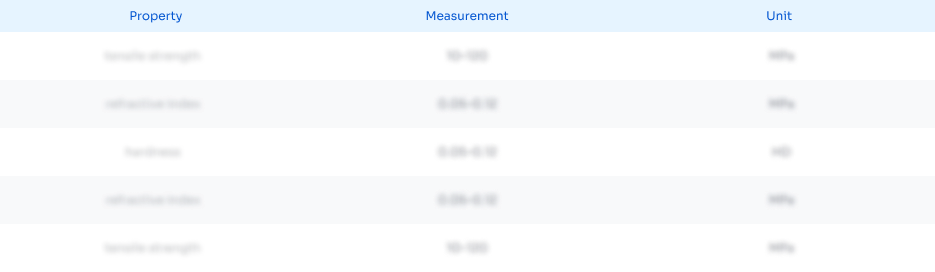
Abstract
Description
Claims
Application Information

- Generate Ideas
- Intellectual Property
- Life Sciences
- Materials
- Tech Scout
- Unparalleled Data Quality
- Higher Quality Content
- 60% Fewer Hallucinations
Browse by: Latest US Patents, China's latest patents, Technical Efficacy Thesaurus, Application Domain, Technology Topic, Popular Technical Reports.
© 2025 PatSnap. All rights reserved.Legal|Privacy policy|Modern Slavery Act Transparency Statement|Sitemap|About US| Contact US: help@patsnap.com