Fairing rigidity and stability determination method
A determination method and technology of the shroud, which are applied in image data processing, special data processing applications, instruments, etc., can solve the problems of inaccurate calculation and few applications, and achieve accurate calculation results, real force conditions, and reasonable judgment methods. Effect
- Summary
- Abstract
- Description
- Claims
- Application Information
AI Technical Summary
Problems solved by technology
Method used
Image
Examples
Embodiment Construction
[0036] The best implementation mode of the present invention will be specifically described below in conjunction with the accompanying drawings.
[0037] A method for determining stiffness and stability of a shroud of the present invention comprises the following steps:
[0038] 1. Establish the geometric model of wind turbine shroud, such as figure 1 , 2 As shown, the upper top cover 1, three 1 / 3 pieces 2 and the hatch 3 of the cover body comprising fiberglass composite materials are connected by the flange bolts of the upper top cover and the three 1 / 3 pieces.
[0039] 2. Properly simplify the geometric model of the wind turbine shroud, delete the small threaded holes and chamfers; import the three-dimensional geometric model of the wind turbine shroud into the finite element analysis software ANSYS Workbench. Since the composite material is an orthotropic material, the pre-processing function of the software is used to model the layup of the shroud, such as image 3 As s...
PUM
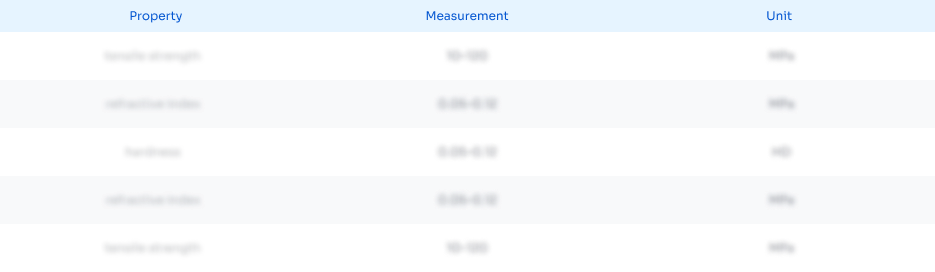
Abstract
Description
Claims
Application Information

- Generate Ideas
- Intellectual Property
- Life Sciences
- Materials
- Tech Scout
- Unparalleled Data Quality
- Higher Quality Content
- 60% Fewer Hallucinations
Browse by: Latest US Patents, China's latest patents, Technical Efficacy Thesaurus, Application Domain, Technology Topic, Popular Technical Reports.
© 2025 PatSnap. All rights reserved.Legal|Privacy policy|Modern Slavery Act Transparency Statement|Sitemap|About US| Contact US: help@patsnap.com