Rapid calculation and design method for radial sliding bearing with axial pressure difference
A technology of radial sliding and design methods, applied in computer-aided design, calculation, design optimization/simulation, etc., can solve problems such as large amount of calculation and complicated design steps of radial sliding bearings
- Summary
- Abstract
- Description
- Claims
- Application Information
AI Technical Summary
Problems solved by technology
Method used
Image
Examples
Embodiment Construction
[0056] The present invention is described in further detail below in conjunction with accompanying drawing:
[0057] Such as figure 1 As shown, the present invention provides a rapid calculation and design method for radial sliding bearings with axial pressure difference, including the following steps:
[0058] 1) According to the known shaft diameter parameters, eccentric parameters and lubrication parameters of the radial sliding bearing, the specific type of bearing is initially selected; and then the various designs including bearing diameter, width, clearance, preload and convergence ratio are selected parameter.
[0059] 2) Take the radial center section of the radial sliding bearing, whose circumferential coordinate is x and axial coordinate is z. The axial pressure distribution of the radial center section is as follows figure 2 shown. In the figure, point A represents the upper end surface of the bearing, and the coordinates are Point B represents the lower end...
PUM
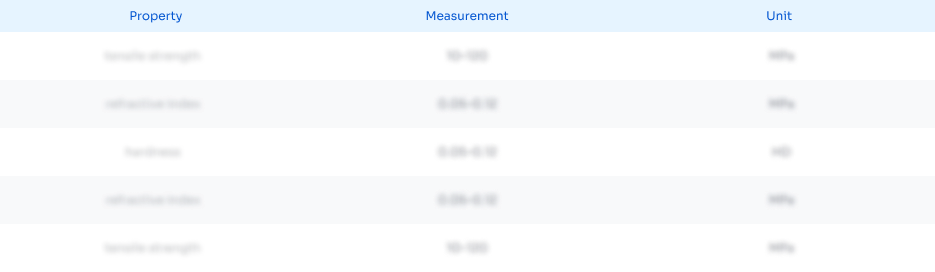
Abstract
Description
Claims
Application Information

- Generate Ideas
- Intellectual Property
- Life Sciences
- Materials
- Tech Scout
- Unparalleled Data Quality
- Higher Quality Content
- 60% Fewer Hallucinations
Browse by: Latest US Patents, China's latest patents, Technical Efficacy Thesaurus, Application Domain, Technology Topic, Popular Technical Reports.
© 2025 PatSnap. All rights reserved.Legal|Privacy policy|Modern Slavery Act Transparency Statement|Sitemap|About US| Contact US: help@patsnap.com