Real-time monitoring device and monitoring method of cable force
A real-time monitoring and cable force technology, applied in the field of bridge engineering and construction, can solve the problems of non-uniform strain changes of point strain sensors, difficulty in ensuring absolute centering of the force measuring ring, and affecting the accuracy of cable force monitoring, etc., to achieve a unique Long-term weather resistance, unique anti-electromagnetic interference ability, and stable monitoring results
- Summary
- Abstract
- Description
- Claims
- Application Information
AI Technical Summary
Problems solved by technology
Method used
Image
Examples
Embodiment Construction
[0033] The specific structure and embodiments of the present invention will be further described below with reference to the accompanying drawings, but the protection scope of the present invention should not be limited by this.
[0034] like figure 1 and figure 2As shown, a real-time monitoring device for cable force includes a force measuring ring 3 and 8 long gauge fiber grating strain sensors 13. The force measuring ring 3 is a hollow ring, which includes a first force bearing ring 10, a second The force-receiving ring 11 and the side wall 15 are provided with axial grooves on the side wall 15 to form a narrow column 12 for installing the sensor. In this embodiment, the number of narrow columns 12 is 8, and each narrow column 12 is installed on the One long-gauge length fiber grating strain sensor 13, generally more than four long-gauge length fiber grating strain sensors 13 can obtain stable data. The long gauge length fiber grating strain sensor 13 is firmly connected...
PUM
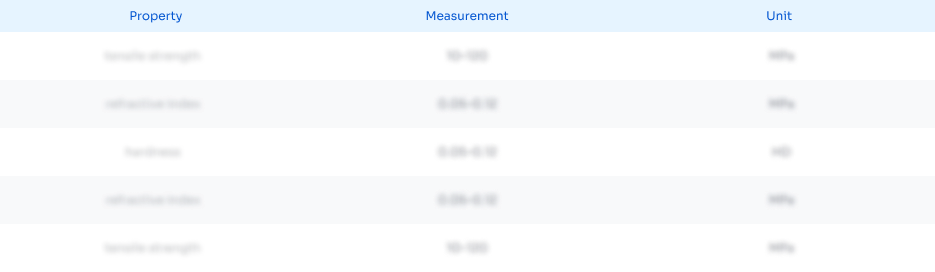
Abstract
Description
Claims
Application Information

- R&D
- Intellectual Property
- Life Sciences
- Materials
- Tech Scout
- Unparalleled Data Quality
- Higher Quality Content
- 60% Fewer Hallucinations
Browse by: Latest US Patents, China's latest patents, Technical Efficacy Thesaurus, Application Domain, Technology Topic, Popular Technical Reports.
© 2025 PatSnap. All rights reserved.Legal|Privacy policy|Modern Slavery Act Transparency Statement|Sitemap|About US| Contact US: help@patsnap.com