Double-front-baffle three-cavity brush seal structure
A technology of brush seals and front baffles, applied in the direction of leakage prevention, engine components, machines/engines, etc., can solve problems affecting the service life of brush seals, aggravate the friction and wear between the brush tip and the rotor, and reduce airflow Direct leakage, avoiding friction, weakening the effect of lateral flow of airflow
- Summary
- Abstract
- Description
- Claims
- Application Information
AI Technical Summary
Problems solved by technology
Method used
Image
Examples
Embodiment 1
[0016] Embodiment 1: see figure 1 It is a double front baffle three-cavity brush seal structure, the brush seal includes a first front baffle 1, a second front baffle 2, a first front cavity 3, a second front cavity 4, a rear baffle Plate 5 , rear cavity 6 , welding zone 7 , brush bundle 8 . The first front baffle 1, the second front baffle 2 and the rear baffle 5 are respectively located on both sides of the brush tow 8, and the inner diameter ends of the second front baffle 2 and the rear baffle 5 have protrusions and inverted horn. A first front cavity exists between the double front plates, a second front cavity 4 exists between the second front baffle plate 2 and the brush filament bundle 8, and a rear cavity exists between the rear baffle plate and the brush filament bundle. The function of the first front cavity is to weaken the lateral flow of high-pressure gas before entering the brush bundle, and the function of the second front cavity and the rear cavity is to red...
Embodiment 2
[0017] Example 2: see figure 1 , as an improvement of the present invention, the thickness of the first front baffle 1 is 0.5-0.9mm, the protection height is 2mm-4mm and does not exceed the protection height of the second front baffle; the thickness of the second front baffle is 0.4mm ~0.8mm, the protection height is 3mm~4mm; the thickness of the rear baffle is 0.3mm~0.7mm, the protection height is 1mm~3mm and does not exceed the protection height of the first front baffle; the axial distance of the first front cavity is 1mm~ 2.5mm, the axial distance between the second front cavity is 0.5mm-0.9mm, and the axial distance between the rear cavity is 1mm-1.5mm; the axial distance between the brush filament bundle and the protrusion at the inner diameter end of the rear baffle is less than 0.3mm. The protection heights of the three baffles and the axial spacing of the three chambers are adjusted according to the shape of the rotor and the application site to achieve the best seali...
PUM
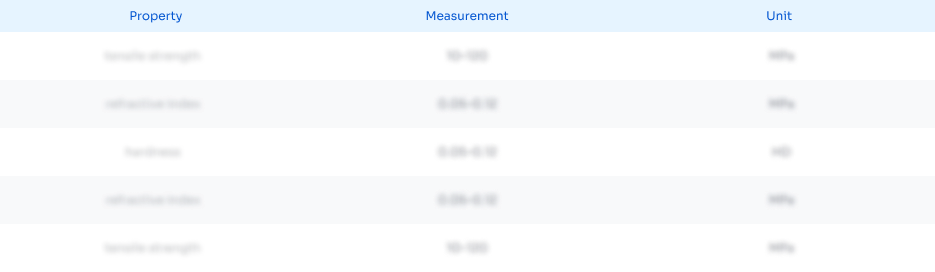
Abstract
Description
Claims
Application Information

- R&D Engineer
- R&D Manager
- IP Professional
- Industry Leading Data Capabilities
- Powerful AI technology
- Patent DNA Extraction
Browse by: Latest US Patents, China's latest patents, Technical Efficacy Thesaurus, Application Domain, Technology Topic, Popular Technical Reports.
© 2024 PatSnap. All rights reserved.Legal|Privacy policy|Modern Slavery Act Transparency Statement|Sitemap|About US| Contact US: help@patsnap.com