Automatic battery box unmanned production line and process
A battery box and production line technology, which is applied in the battery box automatic unmanned production line and its process field, can solve the problems of low automation, low production efficiency, lack of automatic battery box trimming, detection and packaging, etc., and achieve high space utilization , Improve efficiency, efficient and reasonable production process
- Summary
- Abstract
- Description
- Claims
- Application Information
AI Technical Summary
Problems solved by technology
Method used
Image
Examples
Embodiment 1
[0069] Such as Figure 1 to Figure 14 As shown, an automated unmanned production line for battery boxes includes at least one production part 1 and a packing part 2; the discharging end of the production part 1 is provided with a conveyor line 21, and the production part 1 includes several transmission directions along the conveyor line 21 The linearly arranged production modules 11 are automatically processed, shaped, trimmed, inspected, and discarded by each production module 11, and the output battery box 10 is transferred to the conveyor line 21, and is driven by the conveyor line 21 to be transported to the packaging part 2 before the battery The boxes 10 are arranged side by side along the width direction of the conveying line 21; the packing part 2 is arranged at the end of the conveying line 21, which includes at least one stacking part 22 and a grabbing mechanism 23 which are located on the same straight line as the conveying line 21. The grabbing mechanism 23 transfer...
Embodiment 2
[0094] Such as Picture 9 with 10 As shown in the figure, the components that are the same as or corresponding to those in the first embodiment use the same reference numerals as those in the first embodiment. For brevity, only the differences from the first embodiment are described below. The difference between the second embodiment and the first embodiment is that the four corners of the positioning groove 613 are provided with arc-shaped through grooves 615, and the upper ends of the four sides thereof are provided with guiding stoppers 616.
[0095] In this embodiment, arc-shaped through slots are provided at the four corners of the positioning groove 613 so that the four corners of the battery box can be prevented from rubbing against the inner wall of the positioning groove during the process of putting the battery box into the positioning groove. The collision can further ensure the quality of the battery box.
Embodiment 3
[0097] Such as Figure 15 As shown,
[0098] An automated unmanned production process for battery boxes includes the following production process steps:
[0099] a. In the production part, the production module automatically processes and shapes the battery box, and performs trimming, testing and rejection of the processed battery box;
[0100] b. In the transmission part, the battery boxes that have been rejected in step a are transferred to the conveyor line, and are driven by the conveyor line to the packing station. During the transmission, the battery boxes are arranged side by side along the width of the conveyor line;
[0101] c. The packing part, the battery box transferred to the packing station in the step b is transferred to the stacking part for packing by the grabbing mechanism.
[0102] Further, in the step c, before the grab mechanism grabs the battery box, the battery box first passes through the sorting area to complete the sorting of the battery box by side pushing.
[...
PUM
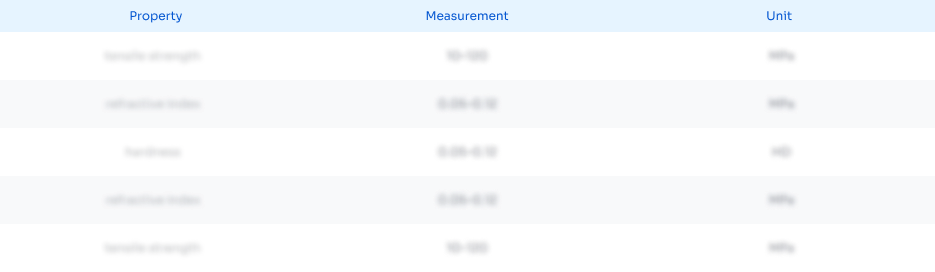
Abstract
Description
Claims
Application Information

- R&D Engineer
- R&D Manager
- IP Professional
- Industry Leading Data Capabilities
- Powerful AI technology
- Patent DNA Extraction
Browse by: Latest US Patents, China's latest patents, Technical Efficacy Thesaurus, Application Domain, Technology Topic, Popular Technical Reports.
© 2024 PatSnap. All rights reserved.Legal|Privacy policy|Modern Slavery Act Transparency Statement|Sitemap|About US| Contact US: help@patsnap.com