Friction stir welding line forming prediction optimization method based on numerical simulation and deep learning
A welding seam forming and friction stir technology, which is used in electrical digital data processing, special data processing applications, instruments, etc., can solve the problems of weak repeatability, poor welding seam forming, and roughness, so as to improve accuracy and reduce material consumption. and time cost, the effect of avoiding time
- Summary
- Abstract
- Description
- Claims
- Application Information
AI Technical Summary
Problems solved by technology
Method used
Image
Examples
Embodiment 1
[0051] A predictive optimization method for friction stir weld formation based on numerical simulation and deep learning, such as figure 1 As shown, the friction stir weld forming prediction optimization method includes:
[0052] Step 1. Optionally, according to actual production requirements, initially set at least three simulation tests for friction stir welding seam forming as the data basis of the numerical simulation model and the test set of the deep learning model of the Generative Adversarial Network (Generative Adversarial Network), and then generate Adversarial network deep learning model;
[0053] Step 2. Establish a numerical simulation model according to the given actual working conditions and material physical parameters, and calculate the distribution of the material flow field and temperature field during the welding process;
[0054] Step 3. According to the material flow field and temperature field distribution obtained in step 2, combined with the unidirect...
PUM
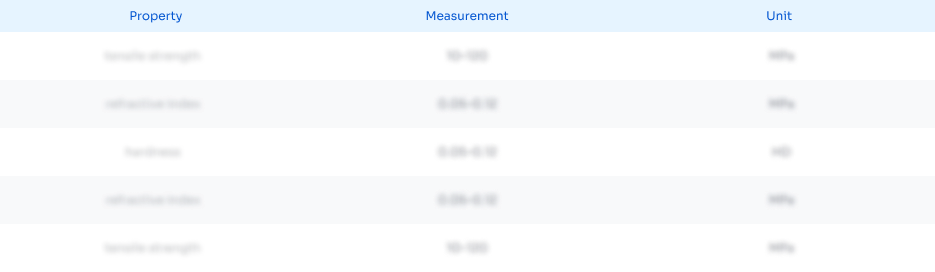
Abstract
Description
Claims
Application Information

- R&D
- Intellectual Property
- Life Sciences
- Materials
- Tech Scout
- Unparalleled Data Quality
- Higher Quality Content
- 60% Fewer Hallucinations
Browse by: Latest US Patents, China's latest patents, Technical Efficacy Thesaurus, Application Domain, Technology Topic, Popular Technical Reports.
© 2025 PatSnap. All rights reserved.Legal|Privacy policy|Modern Slavery Act Transparency Statement|Sitemap|About US| Contact US: help@patsnap.com