Rotary robot welding fixture and working method thereof
A robotic welding and rotary technology, applied in welding equipment, auxiliary welding equipment, welding/cutting auxiliary equipment, etc., can solve the problems of low utilization of space, time-consuming and laborious, low degree of automation, etc., and achieve accurate welding position. , the use of time-saving and labor-saving, high degree of automation effect
- Summary
- Abstract
- Description
- Claims
- Application Information
AI Technical Summary
Problems solved by technology
Method used
Image
Examples
Embodiment Construction
[0046] The technical solutions of the present invention will be clearly and completely described below in conjunction with the embodiments. Apparently, the described embodiments are only some of the embodiments of the present invention, not all of them. Based on the embodiments of the present invention, all other embodiments obtained by persons of ordinary skill in the art without creative efforts fall within the protection scope of the present invention.
[0047] see Figure 1-14 As shown, a rotary robot welding fixture includes a swing table 1, a front clamp seat 2, a rear chuck 3 and a side pressure seat 4, the front clamp seat 2 is arranged above the swing table 1, and the front clamp seat 2 is a A circular rear chuck 3 is arranged on the side, and several side pressure seats 3 are arranged on the edge of the rear chuck 3 in an equal arc;
[0048] A first motor 8 is arranged above the front clamp seat 2, and a rotating plate 9 is connected to the top of the first motor 8,...
PUM
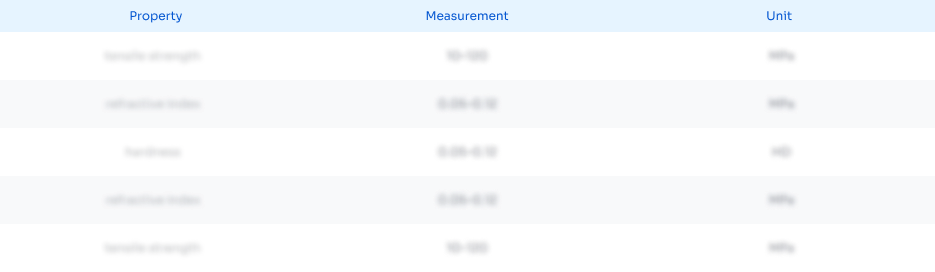
Abstract
Description
Claims
Application Information

- R&D
- Intellectual Property
- Life Sciences
- Materials
- Tech Scout
- Unparalleled Data Quality
- Higher Quality Content
- 60% Fewer Hallucinations
Browse by: Latest US Patents, China's latest patents, Technical Efficacy Thesaurus, Application Domain, Technology Topic, Popular Technical Reports.
© 2025 PatSnap. All rights reserved.Legal|Privacy policy|Modern Slavery Act Transparency Statement|Sitemap|About US| Contact US: help@patsnap.com