Method and device for preparing reagent hydrochloric acid
A technology of reagent hydrochloric acid and reagent grade, applied in the field of preparation of reagent hydrochloric acid, can solve the problems of no continuous large-scale production, liquid pollution to the environment, difficult processing, etc., and achieve continuous and stable large-scale production, simple production process, and save removal. Effects of miscellaneous devices
- Summary
- Abstract
- Description
- Claims
- Application Information
AI Technical Summary
Problems solved by technology
Method used
Image
Examples
Embodiment 1
[0026] A kind of preparation method of reagent hydrochloric acid
[0027] Chlorine gas with a purity of 98.6% (volume ratio), an oxygen content of 0.3%, and a flow rate of 200Nm³ / h passes through the chlorine buffer tank (1) and enters the graphite synthesis furnace with a purity of 99.8% (volume ratio) and a flow rate of 215Nm³ / h The hydrogen gas enters the graphite synthesis furnace (3) after passing through the hydrogen buffer tank (2). The chlorine gas and hydrogen gas entering the synthesis furnace burn and react in the furnace to generate hydrogen chloride gas, which is cooled to below 40°C by the hydrogen chloride cooler (4) and enters the hydrogen chloride distribution table (5). The outlet pressure of the graphite synthesis furnace is controlled at 33kPa. Hydrogen chloride (flow rate is 423Nm³ / h, purity is 94.9%, free chlorine content is less than 0.2ppm) from distribution platform (5) enters into I-level falling film absorption tower (6), and is absorbed in the tower...
Embodiment 2
[0030] A kind of preparation method of reagent hydrochloric acid
[0031] Chlorine gas with a purity of 98.5% (volume ratio), an oxygen content of 0.3%, and a flow rate of 200Nm³ / h passes through the chlorine buffer tank (1) and enters the graphite synthesis furnace with a purity of 99.8% (volume ratio) and a flow rate of 215Nm³ / h The hydrogen gas enters the graphite synthesis furnace (3) after passing through the hydrogen buffer tank (2). The chlorine gas and hydrogen gas entering the synthesis furnace burn and react in the furnace to generate hydrogen chloride gas, which is cooled to below 40°C by the hydrogen chloride cooler (4) and enters the hydrogen chloride distribution table (5). The outlet pressure of the graphite synthesis furnace is controlled at 15kPa. Hydrogen chloride (flow rate is 420Nm³ / h, purity is 94.5%, free chlorine content is less than 0.2ppm) from the distribution table (5) enters the I-level falling film absorption tower (6), and is absorbed in the tower...
Embodiment 3
[0034] A kind of preparation method of reagent hydrochloric acid
[0035] Chlorine gas with a purity of 98.8% (volume ratio), an oxygen content of 0.3%, and a flow rate of 200Nm³ / h passes through the chlorine buffer tank (1) and enters the graphite synthesis furnace with a purity of 99.9% (volume ratio) and a flow rate of 215Nm³ / h The hydrogen gas enters the graphite synthesis furnace (3) after passing through the hydrogen buffer tank (2). The chlorine gas and hydrogen gas entering the synthesis furnace burn and react in the furnace to generate hydrogen chloride gas, which is cooled to below 40°C by the hydrogen chloride cooler (4) and enters the hydrogen chloride distribution table (5). The outlet pressure of the graphite synthesis furnace is controlled at 50kPa. Hydrogen chloride (flow rate: 425N m³ / h, purity: 95.3%, free chlorine content less than 0.2ppm) from the distribution table (5) enters the first-level falling film absorption tower (6), and is absorbed by the second-...
PUM
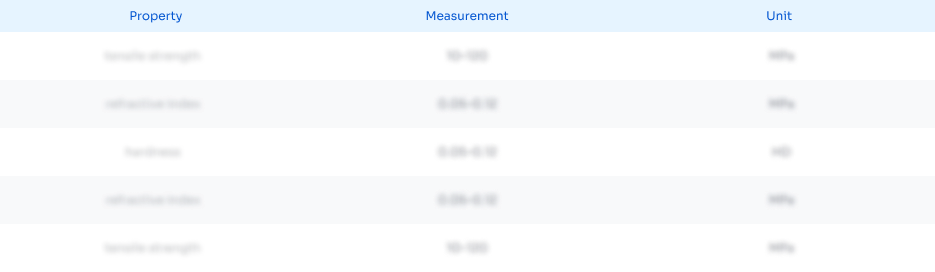
Abstract
Description
Claims
Application Information

- R&D Engineer
- R&D Manager
- IP Professional
- Industry Leading Data Capabilities
- Powerful AI technology
- Patent DNA Extraction
Browse by: Latest US Patents, China's latest patents, Technical Efficacy Thesaurus, Application Domain, Technology Topic, Popular Technical Reports.
© 2024 PatSnap. All rights reserved.Legal|Privacy policy|Modern Slavery Act Transparency Statement|Sitemap|About US| Contact US: help@patsnap.com