Dyeing method for brocade cotton knitted fabric
A dyeing method and a technology for knitted fabrics, which are applied in the dyeing field of nylon-cotton knitted fabrics, can solve problems such as low production efficiency, increased production costs, and complicated technological processes, and achieve the effects of reducing dyeing costs, increasing pass rates, and improving dyeing efficiency
- Summary
- Abstract
- Description
- Claims
- Application Information
AI Technical Summary
Problems solved by technology
Method used
Image
Examples
Embodiment 1
[0041] Nylon cotton knitted fabric: 80S / 1 modal + 40D / 12F nylon semi-gloss filament + 30D spandex double-sided (58% modal 35% nylon 7% spandex), weight 185g / ㎡, width 150cm;
[0042] Equipment: Lixin ECO-38;
[0044]
[0045] Bath ratio: 1:8
[0046] Such as image 3 , after the pre-treatment, put the polyamide-cotton knitted loose cloth into the Fong’s ECO-38 dyeing machine, raise the temperature to 40°C, add leveling agent 723, and Yuanming powder, and dilute the dye in the auxiliary vat by 1 / 2-1 / 3 After mixing evenly, make a dye solution, pump it into the main vat in a quantitative manner of 70% according to the Dosing curve. , keep warm for 30min, then cool down to 60℃ at 0.8℃ / min, run for 10min, add soda ash (inject 1 / 3 according to the Dosing curve at 50% quantitative mode for the first time, and the injection time is 20min, the second time according to the Dosing curve at 50% % Quantitative way to inject 2 / 3, the injection time is 20min), ...
Embodiment 2
[0048] Nylon cotton knitted fabric: 80S / 1 modal + 40D / 12F nylon semi-gloss filament + 30D spandex double-sided (58% modal 35% nylon 7% spandex), weight 185g / ㎡, width 150cm;
[0049] Equipment: Lixin ECO-38;
[0051]
[0052] Bath ratio: 1:6
[0053] After the pretreatment, put the polyamide-cotton knitted fabric loose cloth into the Fong’s ECO-38 dyeing machine, raise the temperature to 40°C, add leveling agent 723 and sodium sulfate, and dilute the dye in the auxiliary vat by 1 / 2-1 / 3 according to the above formula After mixing evenly, make a dye solution, pump it into the master vat in a quantitative manner of 70% according to the Dosing curve. Insulate for 30 minutes, then cool down to 58°C at 0.8°C / min, run for 10 minutes, add soda ash (the first time according to the Dosing curve, inject 1 / 3 in a quantitative manner of 50%, the injection time is 20min, and the second time according to the Dosing curve at 50% Inject 2 / 3 in a quantitative way, t...
Embodiment 3
[0055] Nylon cotton knitted fabric: 80S / 1 modal + 40D / 12F nylon semi-gloss filament + 30D spandex double-sided (58% modal 35% nylon 7% spandex), weight 185g / ㎡, width 150cm;
[0056] Equipment: Lixin ECO-38;
[0058]
[0059]
[0060] Bath ratio: 1:8
[0061] After the pretreatment, put the polyamide-cotton knitted fabric loose cloth into the Fong’s ECO-38 dyeing machine, raise the temperature to 40°C, add leveling agent 723 and sodium sulfate, and dilute the dye in the auxiliary vat by 1 / 2-1 / 3 according to the above formula After mixing evenly, make a dye solution, pump it into the main vat in a 70% quantitative manner according to the Dosing curve. Insulate for 30 minutes, then cool down to 60°C at 0.8°C / min, run for 10 minutes, add soda ash (the first time according to the Dosing curve, inject 1 / 3 in a quantitative manner of 50%, the injection time is 20min, and the second time according to the Dosing curve at 50% Inject 2 / 3 in a quantitative...
PUM
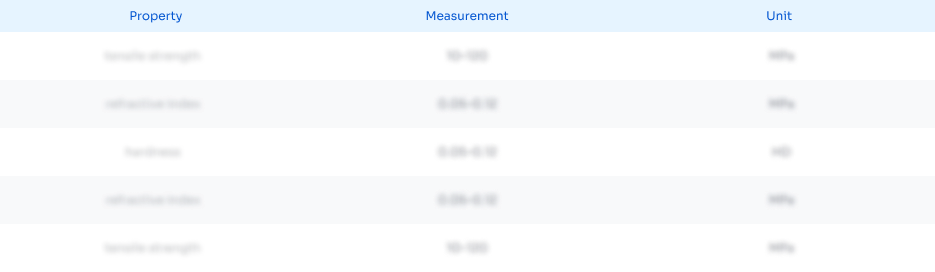
Abstract
Description
Claims
Application Information

- R&D Engineer
- R&D Manager
- IP Professional
- Industry Leading Data Capabilities
- Powerful AI technology
- Patent DNA Extraction
Browse by: Latest US Patents, China's latest patents, Technical Efficacy Thesaurus, Application Domain, Technology Topic, Popular Technical Reports.
© 2024 PatSnap. All rights reserved.Legal|Privacy policy|Modern Slavery Act Transparency Statement|Sitemap|About US| Contact US: help@patsnap.com