Waveguide filter blank body forming mold and its technology
A technology for waveguide filters and forming molds, which is applied in the direction of molds, forming indenters, ceramic forming machines, etc., and can solve problems such as blind holes that cannot be formed, cracks, and missing corners in finished embryos
- Summary
- Abstract
- Description
- Claims
- Application Information
AI Technical Summary
Problems solved by technology
Method used
Image
Examples
Embodiment 1
[0049] refer to figure 1 As shown, the present invention discloses a waveguide filter blank forming mold, comprising an upper mold 2, a middle mold 4, a lower mold 6, an upper mold mandrel 10 and a lower mold mandrel 12; the middle mold 4 has a mold cavity 8 , the above-mentioned mold cavity 8 is filled with powder for pressing and forming an embryo body; the middle mold 4 has an upper mold channel and a lower mold channel that are all communicated with the mold cavity 8, and the other end of the upper mold channel extends to the upper mold of the middle mold surface, the other end of the lower mold channel extends to the lower surface of the middle mold. Above-mentioned upper die 2 and lower die 6 are respectively arranged directly above and directly below middle die 4; The bottom is embedded in the middle mold 4 along the channel of the upper mold and pressurized to dry-press the powder in the mold cavity 8 into an embryo body. The above-mentioned lower mold mandrel 12 is ...
Embodiment 2
[0055] This embodiment discloses a waveguide filter blank forming process, which uses the blank forming mold of Embodiment 1 to physically dry press the waveguide filter blank. The initial state of the forming mold is: ①The top of the lower mold 6 is along the bottom The mold channel is embedded inside the middle mold 4 to block the above-mentioned mold cavity 8; ②The bottom of the upper mold 6 is located directly above the upper mold channel and does not touch the middle mold 4; ③The mandrel 12 of the lower mold fixed on the mandrel base 14 passes through Enter the lower mold 6; ④The upper mold mandrel 10 fixed on the mandrel base 14 penetrates the upper mold 2; ⑤The upper mold 2, the middle mold 4, the lower mold 6, the upper mold mandrel 10 and the lower mold mandrel 12 are connected to the driver, and can rise or fall independently under the drive of the driver; the steps of dry pressing the waveguide filter body based on the molding mold are as follows:
[0056] (1) Under...
PUM
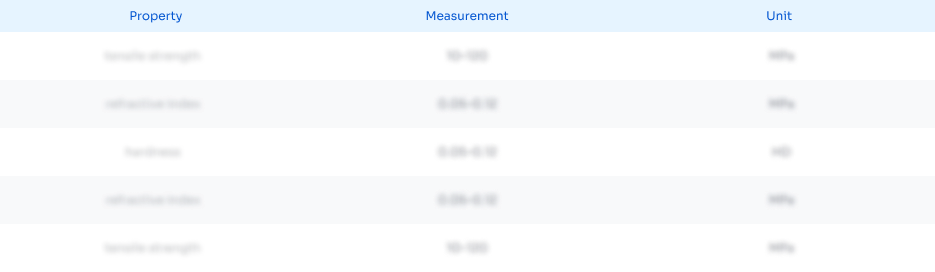
Abstract
Description
Claims
Application Information

- R&D
- Intellectual Property
- Life Sciences
- Materials
- Tech Scout
- Unparalleled Data Quality
- Higher Quality Content
- 60% Fewer Hallucinations
Browse by: Latest US Patents, China's latest patents, Technical Efficacy Thesaurus, Application Domain, Technology Topic, Popular Technical Reports.
© 2025 PatSnap. All rights reserved.Legal|Privacy policy|Modern Slavery Act Transparency Statement|Sitemap|About US| Contact US: help@patsnap.com