Industrial robot based on AGV
An industrial robot and cleaning technology, which is applied in the direction of manipulators, manufacturing tools, program-controlled manipulators, etc., can solve the problems of not being able to clean up impurities such as dust and dirt on the surface of goods, single function, and reduce production efficiency, so as to save the cost of surface cleaning The process and function are highly integrated, and the effect of improving production efficiency
- Summary
- Abstract
- Description
- Claims
- Application Information
AI Technical Summary
Problems solved by technology
Method used
Image
Examples
Embodiment Construction
[0034] In order to more clearly illustrate the technical solutions in the embodiments of the present invention or the prior art, the drawings and technical solutions that need to be used in the description of the embodiments or the prior art will be briefly introduced below. Obviously, the following descriptions The drawings are only some embodiments of the present invention, and those skilled in the art can obtain other drawings according to these drawings without any creative effort.
[0035] The present invention will be further described below in conjunction with the accompanying drawings.
[0036] Such as Figure 1 to Figure 11 As shown, an AGV-based industrial robot provided in this embodiment includes an AGV trolley 1, a control unit 2 electrically connected to the AGV trolley 1, and two objects installed on both sides of the AGV trolley 1 for gripping objects. The clamping mechanism 3, the transport cleaning track set 4 arranged between the two clamping mechanisms 3 f...
PUM
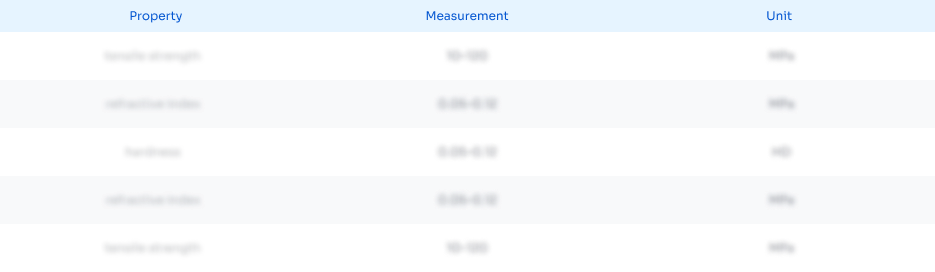
Abstract
Description
Claims
Application Information

- R&D
- Intellectual Property
- Life Sciences
- Materials
- Tech Scout
- Unparalleled Data Quality
- Higher Quality Content
- 60% Fewer Hallucinations
Browse by: Latest US Patents, China's latest patents, Technical Efficacy Thesaurus, Application Domain, Technology Topic, Popular Technical Reports.
© 2025 PatSnap. All rights reserved.Legal|Privacy policy|Modern Slavery Act Transparency Statement|Sitemap|About US| Contact US: help@patsnap.com