Continuous coking device and process
A coking device and process technology, applied in the field of coking, can solve the problems of long coking time, difficult treatment, unorganized discharge of coke oven, etc., and achieve the effect of fast coking speed, simple process and uniform coking
- Summary
- Abstract
- Description
- Claims
- Application Information
AI Technical Summary
Problems solved by technology
Method used
Image
Examples
Embodiment 1
[0026] Embodiment 1: The continuous coking process is as follows.
[0027] 12% gas coal + 10% lean coal + 10% anthracite + 18% 1 / 3 coking coal + 10% fat coal + 36% coking coal + 4% asphalt binder, mix and crush, and the proportion of ≤3mm particle size is greater than 90 %, cold-pressed into briquettes with a diameter of 60mm by a press. The shaped coal is evenly distributed on the conveying device (9) of the continuous coking furnace through the shaped coal storage tank (6) in a single-layer distribution state; the conveying device (9) conveys the shaped coal along the conveying direction, and the conveying device The speed is 3mm / s. During the conveying process, the temperature of the combustion channels symmetrically arranged on the upper and lower surfaces of the conveying device is controlled to be 1250°C to heat the molded coal, so that the molded coal is gradually heated up during the conveying process, and the drying, softening, melting, and semi-coke solidification are ...
Embodiment 2
[0028] Embodiment 2: The continuous coking process is as follows.
[0029] 12% gas coal + 10% lean coal + 10% anthracite + 18% 1 / 3 coking coal + 12% fat coal + 38% coking coal, mixed and crushed, of which the proportion of ≤3mm particle size is greater than 90%, and hot pressed by a press into briquettes with a diameter of 60mm. The shaped coal is evenly distributed on the conveying device (9) of the continuous coking furnace through the shaped coal storage tank (6) in a single-layer distribution state; the conveying device (9) conveys the shaped coal along the conveying direction, and the conveying device The speed is 2.25mm / s. During the conveying process, the temperature of the combustion channels symmetrically arranged on the upper and lower surfaces of the conveying device is controlled to be 1150°C to heat the molded coal, so that the molded coal gradually heats up during the conveying process, and completes drying, softening, melting, and semi-coking. The coking proces...
PUM
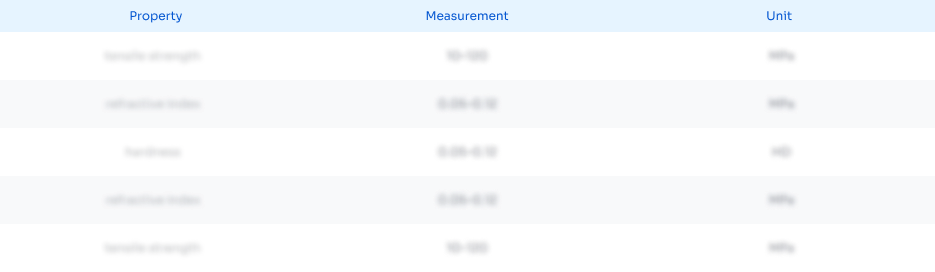
Abstract
Description
Claims
Application Information

- R&D Engineer
- R&D Manager
- IP Professional
- Industry Leading Data Capabilities
- Powerful AI technology
- Patent DNA Extraction
Browse by: Latest US Patents, China's latest patents, Technical Efficacy Thesaurus, Application Domain, Technology Topic, Popular Technical Reports.
© 2024 PatSnap. All rights reserved.Legal|Privacy policy|Modern Slavery Act Transparency Statement|Sitemap|About US| Contact US: help@patsnap.com