Plastic film side face sealing and cutting mold
A plastic film and mold technology, applied in the field of plastic film side sealing and cutting molds, can solve the problems of unsuitability for batch operations, high labor costs, labor-intensive and other problems, and achieves the purpose of expanding the use range of the device, improving the heat sealing quality, and improving the production efficiency. Effect
- Summary
- Abstract
- Description
- Claims
- Application Information
AI Technical Summary
Problems solved by technology
Method used
Image
Examples
Embodiment Construction
[0015] The technical solutions of the present invention will be further described below through specific examples.
[0016] Such as figure 1 and figure 2 As shown, among them, 1 is the plate body, 2 is the heating wire, 3 is the heating tank, 4 is the rotating motor, 5 is the rotating shaft, 6 is the speed regulator, 7 is the upper connecting frame, 8 is the lower connecting frame, 9 is Telescopic cylinder, 10 is the heat sealing plate, 11 is the sealing film heater, 12 is the pressure sensor, 13 is the heat sealing plate, 14 is the heat sealing telescopic frame, 15 is the heat sealing cylinder, 16 is the heat sealing track, 17 is the heating power supply , 18 is a temperature controller, 19 is a temperature sensor, and 20 is a heat seal layer.
[0017] The plastic film side sealing and cutting mold includes a top heat-sealing device, a bottom heat-sealing device, a rotating device and an adjusting device, and the adjusting device is respectively provided with a top heat-se...
PUM
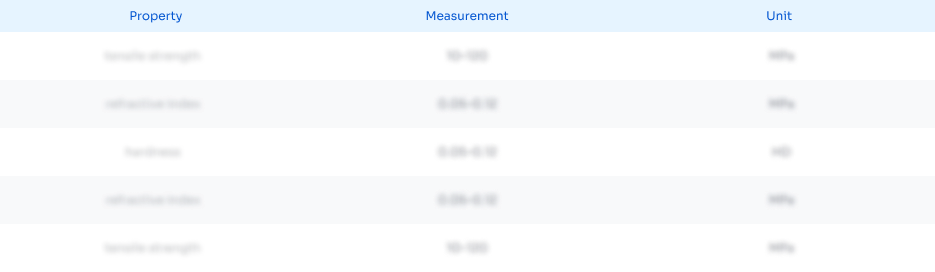
Abstract
Description
Claims
Application Information

- Generate Ideas
- Intellectual Property
- Life Sciences
- Materials
- Tech Scout
- Unparalleled Data Quality
- Higher Quality Content
- 60% Fewer Hallucinations
Browse by: Latest US Patents, China's latest patents, Technical Efficacy Thesaurus, Application Domain, Technology Topic, Popular Technical Reports.
© 2025 PatSnap. All rights reserved.Legal|Privacy policy|Modern Slavery Act Transparency Statement|Sitemap|About US| Contact US: help@patsnap.com