Design method of wing type of rotor wing of micro-miniature type rotor wing UAV (unmanned aerial vehicle) and product
A technology for unmanned rotor and aircraft, which is applied in the direction of aircraft, rotorcraft, instruments, etc., can solve the problems of low propeller aerodynamic efficiency, small size, low lift and drag of airfoil, etc., achieve good engineering practicability, improve aerodynamic efficiency, The effect of increasing the lift coefficient
- Summary
- Abstract
- Description
- Claims
- Application Information
AI Technical Summary
Problems solved by technology
Method used
Image
Examples
Embodiment Construction
[0053] Taking the 15-inch propeller and the operating condition of 2930 revolutions per minute (r / min) as an example (rotor section chord length c = 2.5cm), how to use The above-mentioned design method is used to design the rotor airfoil with high lift-to-drag ratio. The process of the whole design method is as follows: figure 1 As shown, the specific design steps are as follows:
[0054] (1) According to the operating conditions of the three-dimensional rotor, calculate the design state of the airfoil, and select the reference airfoil
[0055] Since the diameter of the blade is 15 inches, that is, 38.1 centimeters, at the 70% radial section,
[0056] Rotation speed: V=2930 / 60×(2πR)×0.7=40.915m / s, where R is the radius of the rotor
[0057] Mach number: Ma=V / a=40.915 / 340.69=0.12, where a is the speed of sound
[0058] Reynolds number: Re=ρVc / μ=1.225×40.915×0.025 / (1.789×10 -5 )=7×10 4 , where ρ is the air density and μ is the air viscosity.
[0059] The angle of attack α...
PUM
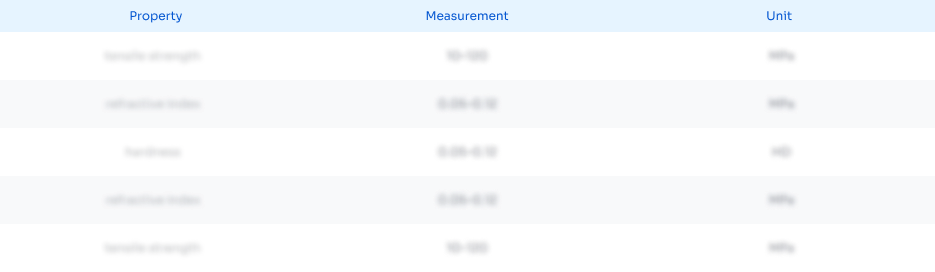
Abstract
Description
Claims
Application Information

- Generate Ideas
- Intellectual Property
- Life Sciences
- Materials
- Tech Scout
- Unparalleled Data Quality
- Higher Quality Content
- 60% Fewer Hallucinations
Browse by: Latest US Patents, China's latest patents, Technical Efficacy Thesaurus, Application Domain, Technology Topic, Popular Technical Reports.
© 2025 PatSnap. All rights reserved.Legal|Privacy policy|Modern Slavery Act Transparency Statement|Sitemap|About US| Contact US: help@patsnap.com