Plastic-covered silk thread production line
A technology for plastic bags and production lines, applied in the field of yarn manufacturing, can solve the problems that the products cannot be directly used in textile machinery, the equipment capacity is small, and the cost is high, so as to reduce the frequency of production line changes, improve production efficiency, and reduce production costs.
- Summary
- Abstract
- Description
- Claims
- Application Information
AI Technical Summary
Problems solved by technology
Method used
Image
Examples
Embodiment 1
[0034] Embodiment 1: as Figure 1 to Figure 3 As shown, the technical scheme adopted by the present invention is as follows: a production line for plastic-coated silk thread, including a creel, a lead frame, an extrusion unit, a diameter measuring instrument, a circulating cooling water tank, a dryer, a tractor and a wire take-up unit, wherein , the above creel is wound with at least two coils of silk thread to be coated, and the thread is exported through the creel; the extruder unit is arranged at intervals on the rear side of the creel, and at least two silk threads derived from the creel pass through the extruder unit At the same time, the extruder unit covers the surface of the wire with a plastic layer to form a plastic-coated wire; the above-mentioned circulating cooling water tanks are arranged at intervals on the rear side of the extruder unit, and when the wire coated with the plastic layer enters the circulating cooling water tank, it passes through the circulating c...
Embodiment 2
[0039] Embodiment 2: as Figure 4 to Figure 6 Shown is Embodiment 2 of the present invention, a production line for plastic-coated silk thread, including a creel, a lead frame, an extruder unit, a diameter measuring instrument, a circulating cooling water tank, a dryer, a tractor, a wire take-up unit and a control unit. Cabinet, wherein, at least two rolls of silk threads to be covered are wound on the above-mentioned creel, and the silk threads are exported through the creel; When extruding the extrusion die of the head, the extruder unit covers the surface of the wire with a plastic layer to form a plastic-coated wire; the above-mentioned circulating cooling water tanks are arranged at intervals on the rear side of the extruder unit, and the wire coated with the plastic layer enters the circulation When cooling the water tank, the solidified plastic layer of the plastic-coated wire is cooled by the circulating cooling water tank; the above-mentioned dryers are arranged at in...
Embodiment 3
[0043] Embodiment 3: as Figure 7 to Figure 9 As shown, it is Embodiment 3 of the present invention, a production line of plastic-coated silk thread, including a creel, a lead frame, an extrusion unit, a diameter measuring instrument, a circulating cooling water tank, a dryer, a tractor, a wire take-up unit and a control unit. Cabinet, wherein, at least two rolls of silk threads to be covered are wound on the above-mentioned creel, and the silk threads are exported through the creel; When extruding the extrusion die of the head, the extruder unit covers the surface of the wire with a plastic layer to form a plastic-coated wire; the above-mentioned circulating cooling water tanks are arranged at intervals on the rear side of the extruder unit, and the wire coated with the plastic layer enters the circulation When cooling the water tank, the solidified plastic layer of the plastic-coated wire is cooled by the circulating cooling water tank; the above-mentioned dryers are arrange...
PUM
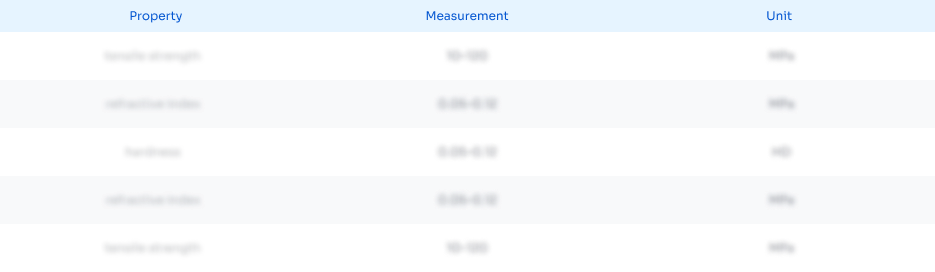
Abstract
Description
Claims
Application Information

- R&D
- Intellectual Property
- Life Sciences
- Materials
- Tech Scout
- Unparalleled Data Quality
- Higher Quality Content
- 60% Fewer Hallucinations
Browse by: Latest US Patents, China's latest patents, Technical Efficacy Thesaurus, Application Domain, Technology Topic, Popular Technical Reports.
© 2025 PatSnap. All rights reserved.Legal|Privacy policy|Modern Slavery Act Transparency Statement|Sitemap|About US| Contact US: help@patsnap.com