A step-by-step stacking method for the initial unbalance of multi-level parts of large-scale high-speed rotary equipment based on convolutional neural network
A technology of convolutional neural network and balance, which is applied in the field of step-by-step stacking of initial unbalance of multi-level components of large-scale high-speed rotary equipment, can solve problems such as large vibration, poor assembly quality, and large unbalance of aero-engine rotors, and achieve improved The effect of efficiency and precision
- Summary
- Abstract
- Description
- Claims
- Application Information
AI Technical Summary
Problems solved by technology
Method used
Image
Examples
Embodiment 1
[0031] Based on the minimization of centroid and mass center, the method of stacking the initial unbalance of multi-level parts of large-scale high-speed rotary equipment step by step, such as figure 1 As shown, the method includes
[0032] Step 1. During the assembly of the multi-stage rotor of the aero-engine, the positioning error of the single-stage rotor will be transmitted and accumulated, which will affect the accumulated eccentricity error of the assembled multi-stage rotor. Determine the eccentricity error transfer matrix caused by the positioning error of the rotors at each stage after the n-stage rotor is assembled, and the eccentricity error transfer matrix is:
[0033]
[0034] Among them, p i is the ideal position vector of the center of the radial measuring surface of the i-th rotor; dp iis the machining error vector of the center position of the radial measuring surface of the i-th rotor; S ri Rotate θ around the Z axis for the i-th stage rotor ri Rotati...
Embodiment 2
[0051] A step-by-step stacking device for the initial unbalance of multi-level parts of large-scale high-speed rotary equipment based on the minimization of centroid and mass center, such as figure 2 As shown, the device includes a base 1, an air bearing shafting 2, a centering and tilting workbench 3, precision force sensors 4a, 4b, 4c, a static balance measuring platform 5, a column 6, and a lower transverse measuring rod 7 , the lower telescopic inductive sensor 8, the upper horizontal measuring rod 9 and the upper lever inductive sensor 10; the air bearing shaft system 2 is nested in the center of the base 1, and the self-aligning and tilting workbench 3 is arranged on the air bearing shaft At the center of the system 2, three precision force sensors 4a, 4b, 4c are evenly arranged on the centering and tilting workbench 3; the static balance measurement platform 5 is on the three precision force sensors 4a, 4b, 4c; the column 6 is distributed on The left side of the air be...
PUM
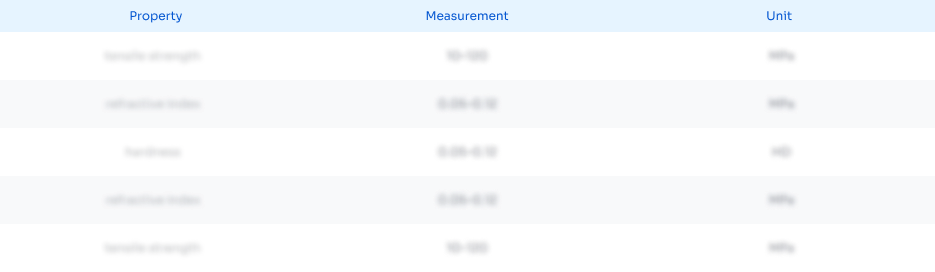
Abstract
Description
Claims
Application Information

- Generate Ideas
- Intellectual Property
- Life Sciences
- Materials
- Tech Scout
- Unparalleled Data Quality
- Higher Quality Content
- 60% Fewer Hallucinations
Browse by: Latest US Patents, China's latest patents, Technical Efficacy Thesaurus, Application Domain, Technology Topic, Popular Technical Reports.
© 2025 PatSnap. All rights reserved.Legal|Privacy policy|Modern Slavery Act Transparency Statement|Sitemap|About US| Contact US: help@patsnap.com