Self-balancing type inertia damper with reciprocating screw rod
A self-balancing, damper technology, used in protective buildings/shelters, building components, earthquake-proof and other directions, can solve the problem that the plate and pendulum dampers do not meet the requirements, cannot use pure tension systems, and cannot be provided by cables. Braking torque and other problems, to achieve the effect of complete separation of damping and stiffness, and high damping coefficient
- Summary
- Abstract
- Description
- Claims
- Application Information
AI Technical Summary
Problems solved by technology
Method used
Image
Examples
Embodiment Construction
[0038] The technical solutions provided by the present invention will be further described below in conjunction with specific embodiments and accompanying drawings. The advantages and features of the present invention will become clearer in conjunction with the following description.
[0039] like Figure 1 to Figure 6 As shown, the present invention provides a self-balancing inertia damper using a reciprocating screw rod, including a reciprocating screw rod 1 , a magnet disk 2 , a conductor disk 3 , a permanent magnet 4 , a screw nut 5 , and a bearing support 6 .
[0040] Wherein, the reciprocating screw rod 1 is a bidirectional threaded screw rod provided with positive and negative threads, and the positive and negative threads are arranged across the entire course on the reciprocating screw rod 1; A screw nut 5 corresponding to the thread is provided, and two screw nuts 5 are respectively engaged and connected with the positive thread and the negative thread of the recipro...
PUM
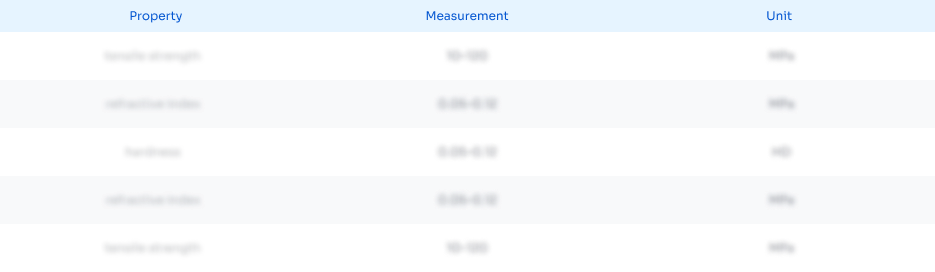
Abstract
Description
Claims
Application Information

- R&D
- Intellectual Property
- Life Sciences
- Materials
- Tech Scout
- Unparalleled Data Quality
- Higher Quality Content
- 60% Fewer Hallucinations
Browse by: Latest US Patents, China's latest patents, Technical Efficacy Thesaurus, Application Domain, Technology Topic, Popular Technical Reports.
© 2025 PatSnap. All rights reserved.Legal|Privacy policy|Modern Slavery Act Transparency Statement|Sitemap|About US| Contact US: help@patsnap.com