Inertial measurement module
A technology of inertial measurement and inertial components, which is applied in directions such as navigation through velocity/acceleration measurement, which can solve the problems affecting the accuracy of inertial measurement, high bias instability scale factor error of MEMS sensors, etc., to simplify the manufacturing process and achieve a compact structure. , to ensure the effect of electrical isolation
- Summary
- Abstract
- Description
- Claims
- Application Information
AI Technical Summary
Problems solved by technology
Method used
Image
Examples
Embodiment Construction
[0022] It is easy to understand that, according to the technical solution of the present invention, those skilled in the art can propose multiple structural modes and implementation modes that can be replaced without changing the essence and spirit of the present invention. Therefore, the following specific embodiments and drawings are only exemplary descriptions of the technical solution of the present invention, and should not be regarded as the entirety of the present invention or as a limitation or restriction on the technical solution of the present invention.
[0023] The directional terms such as up, down, left, right, front, back, front, back, top, and bottom that are mentioned or may be mentioned in this specification are defined relative to the structures shown in the drawings, and they are It is a relative concept, so it may change accordingly according to its different positions and different usage states. Accordingly, these or other directional terms should not be...
PUM
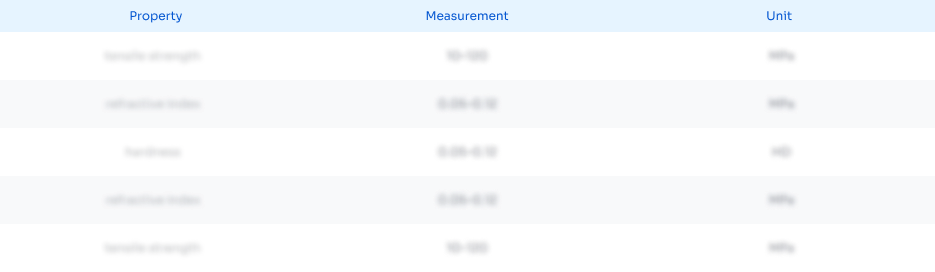
Abstract
Description
Claims
Application Information

- R&D Engineer
- R&D Manager
- IP Professional
- Industry Leading Data Capabilities
- Powerful AI technology
- Patent DNA Extraction
Browse by: Latest US Patents, China's latest patents, Technical Efficacy Thesaurus, Application Domain, Technology Topic, Popular Technical Reports.
© 2024 PatSnap. All rights reserved.Legal|Privacy policy|Modern Slavery Act Transparency Statement|Sitemap|About US| Contact US: help@patsnap.com