Method of transferring forklifts to operate and lift
A technology for forklifts and lifting mechanisms, applied in lifting devices, two-dimensional position/channel control, lifting equipment safety devices, etc., can solve problems such as poor stability and complex structure, and achieve high automation, high work efficiency, Manpower saving effect
- Summary
- Abstract
- Description
- Claims
- Application Information
AI Technical Summary
Problems solved by technology
Method used
Image
Examples
Embodiment 1
[0044] Such as figure 1 , figure 2 as well as image 3 As shown, a system for mobilizing forklift operation has a plurality of AGV bodies. The front end of each AGV body 1 is provided with a transfer lifting mechanism 3, and the transfer lifting mechanism 3 is connected with a fork arm 4. The load lifting mechanism 3 can be composed of a motor and a lead screw, or can be composed of a motor and a transmission chain. It is not limited, and can move in the horizontal direction and the vertical direction at the same time; The traveling driving device 2 is used to control the driving state of the AGV body. Specifically, the traveling driving device 2 includes a traveling mechanism and a steering mechanism. This time, the AGV traditionally adopts the structure of a single front-wheel drive steering three-wheel chassis, and the traveling mechanism adopts Curtis The company's 1232-2211 AC motor controller; the steering mechanism adopts Curtis 1220 DC motor controller; the driven w...
Embodiment 2
[0066] This embodiment is further optimized on the basis of Embodiment 1, specifically a method for mobilizing forklift operation and lifting, including the following steps:
[0067] S0: There are several AGV forklifts and a host computer, each of the AGV forklifts is connected to the host computer in communication, and the host computer is used to send control commands to each AGV forklift and collect data information of each AGV forklift;
[0068] Each of the AGV forklifts includes an AGV body, the front end of the AGV body is provided with a load-shifting lifting mechanism, and the load-shifting lifting mechanism is connected with a fork arm; the bottom of the AGV body is provided with a driving device, which is used To control the driving state of the AGV car body; the AGV car body also has a control system, which includes:
[0069] The execution unit is used to directly send electrical signals to the control circuit of the transfer and lifting mechanism of the AGV body an...
Embodiment 3
[0084] This embodiment is a further optimization made on the basis of Embodiment 2, specifically:
[0085] In the step S41, the following steps are also included:
[0086] S411: Obtain the distance information between each layer of goods and the fork arm, the distance information includes the height value at the lower edge of each layer of shelf pallets, and the height difference between the lower edge and upper edge of each layer of shelf pallets; the control unit according to The distance information controls the lifting height of the transfer lifting mechanism.
[0087] The specific control method is as follows. A position detection sensor and a distance sensor are installed on the fork arm 4. When the position detection sensor detects the lower edge and the upper edge of a shelf beam on a certain layer, the distance sensor detects and records the lower edge of the shelf pallet. The height value H, the height difference X between the lower edge and the upper edge of the sh...
PUM
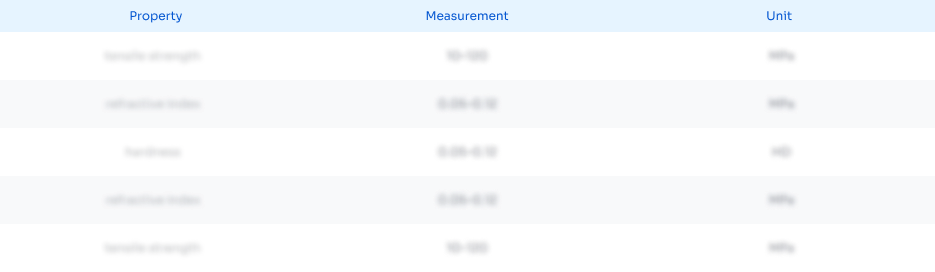
Abstract
Description
Claims
Application Information

- R&D
- Intellectual Property
- Life Sciences
- Materials
- Tech Scout
- Unparalleled Data Quality
- Higher Quality Content
- 60% Fewer Hallucinations
Browse by: Latest US Patents, China's latest patents, Technical Efficacy Thesaurus, Application Domain, Technology Topic, Popular Technical Reports.
© 2025 PatSnap. All rights reserved.Legal|Privacy policy|Modern Slavery Act Transparency Statement|Sitemap|About US| Contact US: help@patsnap.com